Your Trusted Overhead Semi Gantry Crane Crane Manufacturer & Supplier
5 Ton to 32 Ton Double Girder Semi Goliath Crane with Box Girder
Double girder semi goliath crane is a variant of regular goliath crane with one end supported on a leg running on the ground rail and the other end travelling overhead on wall mounted track, therefore also called Single Leg goliath cranes. The single leg semi goliath cranes offers a cost-effective solution for factory or applications with narrow, confined spaces or crowded machinery.
Double girder semi goliath crane 35 ton for your reference
Main Parameters of Double Girder Semi-goliath Cranes
The semi goliath cranes is a small or middle scale goliath crane, which can maximize your space utilization. With single gantry girder design, the capacity of single girder double girder semi-goliath craneis range from 1 ton to 16 ton, and with double gantry girder design, the capacity of the double girder double girder semi-goliath craneis from 3 ton up to 32 tons.Due to the semi-gantry frame design and semi-overhead crane design, the single legged double girder semi-goliath craneowns the advantages of full goliath crane and overhead cranes, widely used for material handling indoors and outdoors.
Main parameters of double girder semi-goliath cranes
- Crane type: BMH double girder semi-goliath cranewith single leg gantry design
- Lifting capacity of semi goliath cranes: 5 ton -32 ton
- Span of semi goliath cranes:5m to 20m, 18m to 35m
- Light Height of semi goliath cranes:6m to 12m,
- Working class of semi goliath cranes:A3, A4
- Ambient temperature of semi goliath cranes:-20℃ to 40℃
Structures & Components of Double Girder Semi-goliath Cranes
Semi goliath crane is a special form developed on the base of goliath crane. The semi goliath crane has one end of gantry girder,move on an overhead runway system elevated like an overhead crane supported on the building of factory workshop and at the other side of gantry girder is supported on one gantry girder moving on a rail like a standard rail mounted goliath crane.
Main Components of Double Girder Semi-goliath Cranes
The double girder semi-goliath craneis mainly consisted of the main crane parts and components such as,crane bridge girder , travelling mechanism, trolley part, electrical control system and other electric part,etc. The main crane parts and components such as , hoist, main girder, crane out-trigger or legs, and ground end beam, are presented for your reference. More information about parts and components of double girder semi-goliath cranes, please feel free to contact us.
Key Components and Structure These cranes typically consist of two main girders running parallel to each other across the span of the crane. The double girder design enhances structural integrity and load-bearing capacity, making them suitable for handling heavier loads compared to single girder alternatives. The semi goliath structure involves one girder end supported by wheels or rails on a ground-level track, while the other end travels on a higher runway beam or rail structure.
Key components include:
- Girders: Two parallel beams that support the hoist and trolley system.
- Hoist and Trolley System: Mechanism responsible for lifting and moving loads horizontally along the girders.
- End Carriages: Support structures at each end of the crane girders, housing wheels or other means of movement.
- Runway Beam or Rails: Provides support and guidance for the crane's movement, ensuring stability and smooth operation.
- Electrical System: Controls for operation, including power supply, control panels, and safety features.
Double Girder Semi Goliath Cranes are designed to optimize lifting capabilities while maintaining flexibility and adaptability in various industrial environments, from manufacturing and logistics to construction and heavy assembly operations.
Electric Hoist :
Dual speed CD1,MD1 wire rope electric hoist, with single girder design & double girder design, can be mounted on single beam & double beam bridge crane, goliath crane and arm cranes.
Main Beam :
Main girder beam is de-rustd by sandblast and painted with zinc rich epoxy primer, and cut by plasma numerical control cutting machine with high precision.
Outrigger :
The rigid outrigger design and flexible outrigger,are all connected by high -tension bolt.
When the length of span is beyond 30m, a flexible leg is need to reduce the lateral thrust of the loaded trolley to the rail.
Ground End Beam :End beam is de-rustd by sandblast and painted with zinc rich epoxy primer, equipted with wheels which is produced in special vacuum casting workshop with more elastic and durable hard-wearing outer surface.
Electric Hoist Trolley or Open Winch Trolley :Dual speed CD1,MD1 wire rope electric hoist, with single girder design & double girder design, can be mounted on single beam & double beam bridge crane, goliath crane and arm cranes.
Main Beam :Main girder beam is de-rustd by sandblast and painted with zinc rich epoxy primer, and cut by plasma numerical control cutting machine with high precision. The ultrasonic or x-ray flaw detection is used to ensure the quality of the butt welding of tension flange.
Outrigger :The rigid outrigger design and flexible outrigger,are all connected by high -tension bolt. When the length of span is beyond 30m, a flexible leg is need to reduce the lateral thrust of the loaded trolley to the rail.
Ground End Beam :End beam is de-rustd by sandblast and painted with zinc rich epoxy primer, equipped with wheels which is produced in special vacuum casting workshop with more elastic and durable hard-wearing outer surface.
Design and Construction Features
In terms of gantry girder designs, the semi goliath cranes can be grouped into single girder double girder semi-goliath craneand double girder double girder semi-goliath cranes. With single gantry girder design, the capacity of single girder double girder semi-goliath craneis range from 1 ton to 16 ton, and with double gantry girder design, the capacity of the double girder double girder semi-goliath craneis from 3 ton up 32 ton. The main parameters of the single girder & double girder double girder semi-goliath cranes are shown as following:
Double Girder Configuration
Double Girder Semi Goliath Cranes are characterized by their robust double girder configuration, which significantly enhances their load-bearing capacity and structural stability. The use of two parallel girders provides greater rigidity compared to single girder cranes, allowing for the efficient handling of heavier loads over longer spans. This configuration also accommodates larger lifting heights and ensures minimal deflection, crucial for precision lifting operations in industrial settings.
Materials Used in Construction
The construction of Double Girder Semi Goliath Cranes involves the use of high-quality materials selected for their durability, strength, and resistance to environmental factors. Common materials include:
- Girder Beams: Typically made from structural steel or alloy steel to withstand heavy loads and minimize structural deformation.
- End Carriages: Constructed from robust steel components to support the girders and ensure stable movement along the runway.
- Rails or Runway Beams: Made from steel or other suitable alloys to provide a secure track for the crane's travel and support.
Additional components such as fasteners, bearings, and electrical wiring are chosen for their reliability and performance under operational conditions. The selection of materials is crucial to ensuring the longevity and operational efficiency of the crane, particularly in demanding industrial environments where reliability and safety are important.
Semi Goliath Crane with Double Girder Box Beams Lifting mechanism of double girder gantry crane with truss gantry design: Hoist or trolley or winch
- Crane type: BMH double girder semi-goliath cranewith single leg gantry design
- Lifting capacity of semi goliath cranes: 5 ton -32 ton
- Span of semi goliath cranes:5m to 20m, 18m to 35m
- Light Height of semi goliath cranes:6m to 12m,
- Working class of semi goliath cranes:A3, A4
- Ambient temperature of semi goliath cranes:-20℃ to 40℃
MG Truss Type Double Girder Gantry Crane 5 ton to 32 ton Lifting mechanism of double girder gantry crane with truss gantry design: Hoist or trolley or winch
- Crane type: BMH double girder semi-goliath cranewith single leg gantry design
- Lifting capacity of semi goliath cranes: 5 ton -32 ton
- Span of semi goliath cranes:5m to 20m, 18m to 35m
- Light Height of semi goliath cranes:6m to 12m,
- Working class of semi goliath cranes:A3, A4
- Ambient temperature of semi goliath cranes:-20℃ to 40℃
Double Girder Semi-goliath Crane Design: Box girder vs. Truss girder
Girder Design:
Box Girder Design: - Features a closed, rectangular cross-section, providing a high degree of torsional rigidity and strength.
- Suitable for handling heavier loads due to its robust construction, making it ideal for demanding industrial applications.
Truss Girder Design: - Consists of an open framework of interconnected triangles, offering high strength with reduced weight.
- Designed to handle moderate loads, offering a balance between strength and lightweight construction.
Typical Applications:
Box Girder Design: - Commonly used in heavy industries such as steel mills, power plants, and large manufacturing facilities.
- Ideal for applications requiring the lifting and movement of large, heavy loads over long distances.
Truss Girder Design: - Suitable for construction sites, warehouses, and maintenance facilities where weight savings are important.
- Effective for lifting and transporting moderate loads, often used in applications where crane weight is a concern.
Load Capacity:
Box Girder Design: - Capable of supporting higher load capacities due to its solid, enclosed structure.
- Often used in scenarios where maximum lifting capacity and minimal deflection are critical.
Truss Girder Design: - Supports moderate load capacities, with a focus on reducing overall crane weight.
- Suitable for applications where load capacities are lower, but efficient material use is essential.
Weight:
Box Girder Design: - Heavier due to the solid, enclosed construction, which contributes to its high load capacity.
- The increased weight requires more substantial support structures and foundations.
Truss Girder Design: - Lighter, as the open framework reduces material usage while maintaining strength.
- The reduced weight makes it easier to install and relocate, with less strain on support structures.
Durability:
Box Girder Design: - Highly durable and resistant to wear and tear, suitable for continuous heavy-duty operations.
- The closed design protects internal components from environmental factors.
Truss Girder Design: - Durable but with a focus on efficient material use, suitable for regular industrial applications.
- The open design may expose internal components to environmental factors, requiring more maintenance.
Flexibility and Customization:
Box Girder Design: - Offers high customization in terms of span, height, and load capacity to meet specific industrial needs.
- Can be tailored to various operational requirements, including specialized lifting tasks.
Truss Girder Design: - Also customizable, with flexibility in designing for specific load capacities and spatial constraints.
- Suitable for applications where weight and material efficiency are prioritized.
Stability and Strength:
Box Girder Design: - Provides superior stability and strength, minimizing deflection under heavy loads.
- Ideal for applications where maintaining structural integrity under high stress is essential.
Truss Girder Design: - Offers good stability with a focus on distributing loads efficiently through the truss structure.
- Effective in applications where reducing material stress and maintaining lightweight construction are important.
Cost:
Box Girder Design: - Generally higher cost due to the increased material use and construction complexity.
- The investment reflects the enhanced strength and load capacity.
Truss Girder Design: - Potentially lower cost due to the reduced material usage and simpler construction.
- The cost-effectiveness reflects the balance between strength and lightweight design.
All in all, the semi gantry cranes with box girder and truss girder designs are different in the following terms
Box Girder Design:
- Pros: High torsional rigidity, suitable for heavy loads, highly durable, customizable, superior stability.
- Cons: Heavier weight, higher cost, requires substantial support structures.
Truss Girder Design:
- Pros: Lightweight, cost-effective, good load distribution, customizable, easier installation.
- Cons: Moderate load capacity, potentially more maintenance, less suitable for very heavy-duty applications.
Both designs offer unique advantages, with the Box Girder design excelling in heavy-duty applications requiring maximum strength and stability, while the Truss Girder design provides a lightweight, cost-effective solution for moderate load handling with efficient material use.
Advantages of Double Girder Semi Goliath Cranes
Double Girder Semi Goliath Cranes offer several distinct advantages that make them a preferred choice in various industrial applications:
Increased Load Capacity Compared to Single Girder Cranes: One of the primary advantages of Double Girder Semi Goliath Cranes is their significantly enhanced load-bearing capacity. The dual girder configuration distributes the load more evenly across the span, allowing these cranes to handle heavier loads compared to their single girder counterparts. This capability is particularly advantageous in industries requiring the lifting and maneuvering of bulky or dense materials, such as manufacturing, steel mills, and shipbuilding.
Enhanced Stability and Rigidity: The double girder design of these cranes provides superior stability and rigidity during operation. By minimizing deflection and sway, Double Girder Semi Goliath Cranes ensure precise positioning and controlled movements, essential for lifting operations that demand accuracy and safety. This structural robustness also contributes to prolonged crane longevity and reduced maintenance requirements, enhancing overall operational efficiency.
Suitable for Outdoor Applications with Uneven Ground: Double Girder Semi Goliath Cranes are well-suited for outdoor environments characterized by uneven or rugged terrain. Unlike fully gantry-supported cranes, which require a level surface for both rails, semi goliath cranes feature one end supported on the ground and the other on a runway beam or rail structure. This design flexibility allows them to operate effectively in yards, construction sites, or open-air facilities where ground conditions may vary, providing versatile lifting solutions without compromising on performance or safety.
These advantages make Double Girder Semi Goliath Cranes indispensable in industries where heavy lifting, stability, and adaptability to outdoor environments are critical considerations.
- Customized design, Compact crane structure, Durable gantry girder design, Great rigidity.
- Good crane performance,Smooth crane starting and stopping,Stable and reliable traveling, Strong ability of lateral load proof.
- Crane installation and operation with high flexibility, Excellent exchange ability for parts and components,.Convenient maintenance,
- Low noise, No pollution,Electricity saves,Less investment
Features of Semi-goliath crane
- Dual speed electric hoist with CD,MD motor, travelling on rail of semi goliath crane.
- Three-in-one motor used on the semi goliath crane to save more working space.
- Best light crane equipped with hard tooth face reducer & three-in-one motor for outdoor or workshop use.
- Lowest space between the top of trolley crab and the trolley rail, 20-30 % less than the traditional type.
- Electric panel with more than 2 million times service life, are used on the semi goliath crane.
- Various protection devices and alarming devices are used to .ensure the security and stability of double girder semi-goliath crane.
Applications and Industries of Semi Goliath Cranes
Double Girder Semi Goliath Cranes find extensive use across various industries and applications due to their robust design and versatile capabilities:
Applications of Double Girder Semi Goliath Cranes for Various Working Environment
Double Girder Semi Goliath Crane for Indoor Use:
Double Girder Semi Goliath Cranes designed for indoor use are versatile solutions for various industrial applications within controlled environments. Featuring a dual girder configuration and ground-level support on one side, these cranes are suitable for factories, warehouses, and manufacturing facilities where overhead space may be limited or where columns and supports cannot accommodate a full gantry structure. Their robust design allows for efficient handling of heavy loads with enhanced stability and precision. These cranes are typically customized to integrate smoothly into existing facility layouts, optimizing workflow efficiency and ensuring reliable material handling operations indoors.
Double Girder Semi Goliath Crane for Outdoor Use:
Double Girder Semi Goliath Cranes tailored for outdoor use are engineered to withstand challenging environmental conditions while providing robust lifting capabilities. With one end supported on the ground and the other on a runway beam or rail structure, these cranes offer flexibility in deployment across construction sites, ports, and outdoor storage yards. They excel in lifting and transporting bulky materials, containers, and structural components, facilitating efficient logistics and construction operations. Weather-resistant materials and corrosion protection measures ensure longevity and reliability in outdoor settings, making them essential for applications requiring durability and adaptability to varying weather conditions.
Double Girder Semi Goliath Crane for Hazardous Use:
Double Girder Semi Goliath Cranes designed for hazardous environments are equipped to operate safely in environments where explosive atmospheres or chemical hazards may be present. These cranes adhere to stringent safety standards and regulatory requirements, incorporating specialized features such as explosion-proof components, spark-resistant materials, and enhanced ventilation systems. They are commonly utilized in industries such as oil refineries, chemical plants, and mining operations where the presence of flammable substances necessitates careful consideration of equipment design and operational protocols. These cranes ensure reliable and secure lifting operations while mitigating risks associated with hazardous materials, prioritizing both personnel safety and operational efficiency.
Applications of Double Girder Semi Goliath Cranes for Various Industrial Sectors
- Heavy-duty Manufacturing and Assembly:In heavy-duty manufacturing facilities, Double Girder Semi Goliath Cranes are essential for lifting and maneuvering large components, machinery, and materials. They excel in industries such as automotive manufacturing, steel production, and aerospace, where precision handling of heavy loads is crucial for assembly processes. These cranes facilitate efficient material flow and streamline production operations, enhancing productivity and minimizing downtime.
- Warehousing and Logistics:Within warehousing and logistics environments, Double Girder Semi Goliath Cranes play a pivotal role in managing inventory, handling oversized goods, and optimizing storage space. Their ability to lift heavy loads across wide spans ensures efficient movement of pallets, containers, and bulk materials within distribution centers and storage facilities. They are also used in automated storage and retrieval systems (AS/RS) to enhance operational efficiency and inventory management.
- Construction Sites and Shipyards: Double Girder Semi Goliath Cranes are indispensable in construction sites and shipyards where they facilitate the lifting and positioning of building materials, prefabricated components, and maritime equipment. Their mobility and adaptability to uneven ground make them ideal for outdoor construction projects, such as bridge construction, building erection, and infrastructure development. In shipyards, these cranes are used for launching vessels, handling ship components, and supporting marine maintenance operations, ensuring safe and efficient maritime logistics.
These applications underscore the versatility and utility of Double Girder Semi Goliath Cranes across diverse industrial sectors, where their robust performance and lifting capabilities contribute to operational efficiency and project success.
Customization Options
Double Girder Semi Goliath Cranes offer a range of customization options to meet specific operational requirements and enhance functionality:
- Span Length and Lifting Height:Customizable span lengths and lifting heights allow Double Girder Semi Goliath Cranes to adapt to varying facility layouts and operational needs. Manufacturers offer configurations tailored to specific project requirements, ensuring optimal coverage and reach within the workspace. This customization capability is crucial in environments where different lifting heights or spans are necessary to accommodate varying load sizes or operational constraints.Hoisting Mechanisms and Speed
- Control:The choice of hoisting mechanisms, such as wire rope hoists or chain hoists, enables customization based on load capacities and operational preferences. Advanced speed control systems, including variable frequency drives (VFDs), provide precise control over lifting and lowering speeds, optimizing productivity and enhancing safety during crane operations. Customizable speed settings accommodate different load conditions and operational environments, ensuring efficient material handling and reduced cycle times.
- Safety Features and Automation:Integration of safety features and automation technologies enhances the operational safety and efficiency of Double Girder Semi Goliath Cranes. Customizable safety features may include overload protection systems, anti-collision devices, emergency stop buttons, and perimeter safety fencing to prevent unauthorized access. Automation options, such as remote control systems, automated load positioning, and diagnostics monitoring, streamline crane operations and minimize manual intervention, improving overall productivity and reducing downtime.
These customization options empower businesses to tailor Double Girder Semi Goliath Cranes to specific operational environments, ensuring optimal performance, safety, and efficiency across diverse industrial applications.
Operational Considerations
Double Girder Semi Goliath Cranes require careful consideration of various operational factors to ensure reliable performance and longevity:
- Maintenance Requirements:Effective maintenance practices are essential to maximize the operational lifespan and reliability of Double Girder Semi Goliath Cranes. Regular inspections, lubrication of moving parts, and timely replacement of wear components such as ropes and brakes are crucial maintenance tasks. Scheduled maintenance programs, including preventive maintenance and routine inspections by qualified technicians, help identify potential issues early and minimize unplanned downtime. Manufacturers often provide maintenance guidelines and service schedules tailored to specific crane models to optimize performance and ensure compliance with safety standards.Power Supply
- Specifications (Voltage, Frequency):Double Girder Semi Goliath Cranes operate on electrical power, requiring specific voltage and frequency specifications to function effectively. Power supply requirements typically include considerations for voltage levels (e.g., 380V, 440V, 480V) and frequency (e.g., 50Hz or 60Hz), depending on regional standards and application needs. Ensuring compatibility with the facility's electrical infrastructure and providing stable power distribution are critical to prevent operational disruptions and equipment damage. Voltage regulation devices and surge protection systems may be employed to safeguard crane electronics and ensure consistent performance under varying power conditions.
- Environmental Factors (Weather Resistance, Corrosion Protection)Environmental conditions, such as exposure to weather elements and corrosive atmospheres, can impact the performance and longevity of Double Girder Semi Goliath Cranes. Manufacturers incorporate weather-resistant materials and corrosion protection measures, such as galvanized coatings, epoxy paints, and stainless steel components, to mitigate the effects of moisture, UV radiation, and chemical exposure. Crane installations in outdoor or maritime environments may require additional protective measures, including climate-controlled cabins, sealing against dust ingress, and periodic surface treatments to maintain structural integrity and prevent premature deterioration.
Addressing these operational considerations ensures that Double Girder Semi Goliath Cranes operate efficiently, sustainably, and safely throughout their service life, supporting uninterrupted industrial operations and minimizing maintenance costs.
Regulatory Compliance and Standards
Compliance with international crane standards and local safety regulations is crucial for ensuring the safe operation and regulatory adherence of Double Girder Semi Goliath Cranes:
International Crane Standards (e.g., ISO, CMAA) ISO Standards: Double Girder Semi Goliath Cranes should comply with relevant ISO standards that define requirements for design, manufacturing, testing, and safety of cranes. Key standards include:
- ISO 4301-1: Cranes - Classification - Part 1: General
- ISO 4306-1: Cranes - Vocabulary - Part 1: General
- ISO 12480-1: Cranes - Design principles for loads and load combinations - Part 1: General principles
- ISO 16881-1: Cranes - Design principles for loads and load combinations - Part 1: General principles
- ISO 16881-2: Cranes - Design principles for loads and load combinations - Part 2: Bridge and gantry cranes
Local Safety Regulations and Inspections - Safety Regulations: Double Girder Semi Goliath Cranes must adhere to local safety regulations and codes specific to the region where they are installed and operated. These regulations often include requirements for crane design, operation, maintenance, and personnel training to ensure workplace safety and prevent accidents.
- Inspections: Regular inspections by qualified personnel are mandatory to verify crane compliance with safety standards and operational integrity. Inspections typically cover structural components, mechanical systems, electrical components, safety devices, and overall operational performance. Inspectors may conduct visual inspections, non-destructive testing (NDT), load testing, and functional tests to assess crane condition and identify potential safety hazards.
- Certification and Documentation: Cranes may require certification from regulatory authorities or third-party inspection agencies to demonstrate compliance with applicable standards and regulations. Documentation such as load charts, operation manuals, maintenance records, and inspection reports must be maintained and readily available for audit purposes.
Adherence to international standards and local regulations ensures that Double Girder Semi Goliath Cranes operate safely, reliably, and legally within industrial environments, promoting worker safety and operational efficiency.
Cost Considerations
When evaluating Double Girder Semi Goliath Cranes, it's essential to consider both the initial investment and ongoing operating costs:
Initial Investment - Capital Cost: The initial investment in Double Girder Semi Goliath Cranes includes the purchase price of the crane itself, which varies based on factors such as load capacity, span length, lifting height, customization options, and manufacturer. Higher load capacities and larger spans typically result in higher initial costs due to increased material and engineering requirements.
- Installation Costs: Installation expenses encompass crane assembly, commissioning, and integration into existing facility infrastructure. Factors influencing installation costs include site preparation, crane foundation requirements, assembly labor, and any necessary modifications to support structures.
- Customization Costs: Additional costs may arise from customization options such as specialized hoisting mechanisms, speed control systems, safety features, and automation technologies tailored to specific operational needs. Customization enhances crane functionality but can incrementally increase initial investment.
Operating Costs - Maintenance Costs: Ongoing maintenance is critical to preserve crane performance and longevity. Maintenance expenses include routine inspections, lubrication, replacement of wear parts (e.g., ropes, bearings), and corrective maintenance to address operational issues. Preventive maintenance programs help minimize downtime and repair costs over the crane's lifespan.
- Energy Consumption: Double Girder Semi Goliath Cranes consume electrical energy during operation, primarily for hoisting, traversing, and auxiliary functions. Energy-efficient designs, such as variable frequency drives (VFDs) for motor control, can reduce energy consumption and operating costs. Monitoring energy usage and implementing energy-saving practices contribute to overall cost savings.
- Operational Efficiency: Efficient crane operation through optimized workflow planning, load scheduling, and operator training enhances productivity and reduces operational costs. Well-trained personnel ensure safe and effective crane utilization, minimizing the risk of accidents and associated downtime.
Total Cost of Ownership (TCO) Assessing the total cost of ownership (TCO) considers both initial investment and ongoing operating expenses to determine the long-term financial impact of owning Double Girder Semi Goliath Cranes. TCO analysis helps stakeholders make informed decisions by balancing upfront expenditures with lifecycle costs and operational benefits.
By carefully evaluating initial investment and operating costs, businesses can optimize budget allocation, maximize crane performance, and achieve cost-effective material handling operations with Double Girder Semi Goliath Cranes.
Comparison with Other Crane Types
Double Girder Semi Goliath Cranes offer distinct advantages over other crane types, including single girder semi goliath cranes, full goliath cranes, and overhead bridge cranes:
Comparison with Single Girder Semi Goliath Cranes - Load Capacity: Double Girder Semi Goliath Cranes typically have higher load capacities than single girder semi goliath cranes due to their dual girder design. This makes them suitable for lifting heavier loads and handling larger spans, providing greater operational flexibility.
- Stability and Rigidity: The double girder configuration enhances structural stability and rigidity, minimizing deflection during lifting operations. This ensures precise load positioning and reduces wear on crane components over time compared to single girder cranes.
- Lifting Height: Double Girder Semi Goliath Cranes can achieve higher lifting heights compared to single girder cranes, making them suitable for applications requiring vertical reach and clearance.
Advantages over Full Goliath Cranes and Overhead Bridge Cranes - Mobility and Flexibility: Double Girder Semi Goliath Cranes offer greater mobility and flexibility compared to full goliath cranes, which require support on both sides of the runway. Semi goliath cranes feature one end supported on the ground and the other on a runway beam or rail structure, allowing them to operate in areas with limited space or uneven terrain.
- Installation and Space Utilization: Full goliath cranes require substantial groundwork and space for installation due to their symmetrical support structure. In contrast, semi goliath cranes require less groundwork and can be installed more quickly, optimizing space utilization in congested or outdoor environments.
- Cost Efficiency: Double Girder Semi Goliath Cranes often offer a cost-effective solution compared to full goliath cranes, balancing higher load capacities and operational flexibility with reduced installation and maintenance costs. They provide a versatile option for applications where full gantry support is unnecessary.
- Operational Adaptability: Overhead bridge cranes operate exclusively on elevated runways and are typically limited by runway length and span. Double Girder Semi Goliath Cranes, with their ground-level support and adjustable runway structure, offer enhanced operational adaptability and accessibility across different work environments.
By comparing these factors, stakeholders can assess the suitability of Double Girder Semi Goliath Cranes relative to single girder semi goliath cranes, full goliath cranes, and overhead bridge cranes based on specific project requirements, operational needs, and budget considerations.
Case Studies and Practical Examples
Real-World Applications and Success Stories - Heavy-Duty Manufacturing: In a large-scale automotive manufacturing facility, Double Girder Semi Goliath Cranes are used for handling heavy components such as engine blocks and chassis assemblies. Their dual girder configuration and high load capacity ensure efficient material flow and support seamless production operations. The cranes facilitate precise positioning and lifting in confined spaces, contributing to increased productivity and operational efficiency.
- Construction and Infrastructure Projects: On a major bridge construction site, Double Girder Semi Goliath Cranes play a crucial role in lifting precast concrete segments and structural elements. Their mobility and adaptability to uneven terrain allow them to maneuver around construction obstacles while maintaining safety and precision during lifting operations. The cranes support timely project completion by enabling rapid assembly and installation of bridge components, minimizing construction delays.
- Shipbuilding and Maritime Industries: In shipyards, Double Girder Semi Goliath Cranes are employed for launching and outfitting vessels. Their robust design and lifting capabilities facilitate the handling of large ship sections and maritime equipment. The cranes ensure efficient workflow and logistics management, supporting shipbuilding projects from keel laying to final outfitting stages. They enhance operational throughput and enable shipyards to meet strict project timelines and delivery schedules.
Challenges Faced and Solutions Implemented - Environmental Conditions: In an outdoor steel fabrication yard, Double Girder Semi Goliath Cranes faced challenges related to exposure to harsh weather conditions and corrosive environments. To mitigate corrosion and ensure crane longevity, protective measures such as epoxy coatings, stainless steel components, and regular maintenance were implemented. These solutions safeguarded crane performance and minimized downtime due to weather-related damage.
- Operational Efficiency: In a logistics warehouse handling diverse cargo types, Double Girder Semi Goliath Cranes encountered challenges related to operational efficiency and load handling variability. Advanced automation features, including automated load positioning systems and real-time monitoring, were integrated to streamline crane operations. These enhancements optimized workflow efficiency, reduced turnaround times, and enhanced overall warehouse productivity.
- Safety and Compliance: During a refinery expansion project, Double Girder Semi Goliath Cranes were required to adhere to stringent safety regulations and compliance standards. Safety features such as anti-collision devices, overload protection systems, and operator training programs were implemented to ensure safe crane operation and mitigate risks associated with heavy lifting activities. Compliance with local safety regulations and regular inspections contributed to maintaining a safe working environment and preventing potential accidents.
These case studies illustrate the diverse applications and success stories of Double Girder Semi Goliath Cranes across different industries, highlighting their versatility, reliability, and capability to overcome operational challenges through innovative solutions and best practices.
Get Your Customized Semi-goliath Crane
Double Girder Semi Goliath Cranes represent a robust solution for diverse industrial applications, offering substantial benefits and considerations for stakeholders in material handling and logistics operations. As evidenced by their widespread adoption across heavy-duty manufacturing, construction projects, and maritime industries, these cranes provide:
- Enhanced Load Capacity and Stability: Double girder configuration enables higher load capacities and improved stability compared to single girder cranes, supporting efficient handling of heavy and oversized materials.
- Flexibility and Mobility: Ground-level support combined with runway structure allows semi goliath cranes to operate in environments with uneven terrain or limited space, providing flexibility in installation and operational deployment.
- Cost Efficiency: While requiring less groundwork and installation effort compared to full goliath cranes, semi goliath cranes offer cost-effective solutions for lifting operations, balancing initial investment with long-term operational benefits.
- Operational Safety and Compliance: Integration of advanced safety features, compliance with international standards (e.g., ISO, CMAA), and adherence to local regulations ensure safe and compliant crane operations, minimizing risks and enhancing workplace safety.
Semi Goliath Crane, Your Economical Material Handling Solution
Semi goliath cranes, the special form of overhead goliath cranes combine the advantages of overhead travelling bridge cranes and goliath cranes, but with higher flexibility than overhead eot crane and lower cost than the standard regular rail goliath crane. Semi goliath crane is a good choice to save investment and space, especially when you are in the following conditions:
- Your plant needs an efficient solution to coordinate forklifts to handle heavy or very long loads to improve safety, efficiency and save time.
- Your lifting volume is moderate which does not need to install an expensive and permanent overhead travelling crane system.
- Your plant has existing overhead cranes, but need an economical and versatile lifting system to supplement the existing crane system.
Semi goliath crane has a widely application for various industrial applications, Generally, semi goliath cranes can be used in the following two typical applications:
- Indoors - Semi goliath cranes is used to cooperate with the the existing overhead bridge cranes to provide more hooks and to improve the productivity of your factory.
- Outdoors - The single leg goliath crane is used outside but near the building, , taking advantage of the existing runway structure, to improve the cost efficient of your building.
All in all, Semi goliath cranes offers your economical material handling solution with lifting capacity up to 32 ton and crane span up to 32 m, which is an excellent alternative solution to expensive overhead cranes. Single leg semi goliath crane is widely used for material handling in open warehouse,mechanical processing workshop, outdoor places, etc. However, standard semi goliath crane is not allowed to be in hazardous environments, such as, the environment of combustible, explosive, dusty and corrosive, etc.
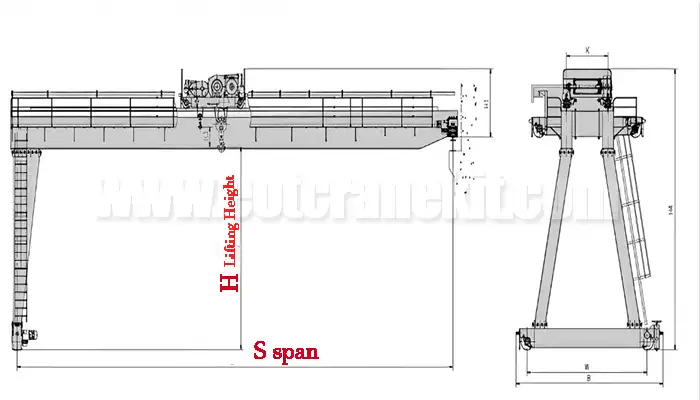
Drawing of semi goliath crane: Span Length and Lifting Height
How to select a double girder semi-goliath cranefor your application? In order to give you suitable semi goliath crane solution and specific crane price promptly, please confirm the following with our goliath crane engineer as much as possible:
- Gantry girder design of double girder semi-goliath crane: Single girder / double girder design? With 1 cantilever/ no cantilever?
- Capacity: ____ ,Span:____, Height of Lift:____,Travelling Length:___
- Power supply: 3 phase___Voltage___ Hz
- Operation: Through Pendant/Radio Remote/Cabin Control?
- Application: Industry type: _____, Indoor/Outdoor: ____. Loads: _______
- Size of Existing Rail: ___
Free consultation of semi goliath crane is available.Any questions or problem are welcomed.Please just leave a message below and reply will be given within 24 hours. Get your custom designed semi goliath crane.