Your Trusted Overhead Crane System Manufacturer & Supplier
Overhead Crane Systems 1 to 320 Ton for Your Material Handling
Crane System Types, Applications, and Crane Buyer Considerations
Explore various crane systems, their subsystems, capacities, features, applications, and key considerations for making informed purchasing decisions.
Overhead crane system guide is designed to help you understand crane systems comprehensively. It covers the different types of cranes, their key components, and essential factors to consider when making a purchasing decision. By following this guide, you can navigate the complexities of crane systems and find solutions that meet your specific needs.
Selecting the right crane system is crucial for maximizing efficiency and safety in your operations. The right choice can streamline workflows, reduce downtime, and improve overall productivity. Making an informed decision not only minimizes long-term costs but also ensures that your operations run smoothly, adhering to safety regulations and operational standards.
Crane systems play a vital role in many industries, including manufacturing, construction, logistics, and warehousing. In manufacturing, cranes facilitate the movement of heavy components, while in construction, they help lift materials to heights. In logistics and warehousing, cranes optimize storage and retrieval processes. Their adaptability makes them invaluable for efficient material handling, significantly boosting productivity across various sectors.
Overivew of Overhead Crane Systems
Definition of Crane Systems Crane systems are specialized mechanical devices designed for the efficient lifting, moving, and lowering of heavy loads across various industrial applications. They play a crucial role in enhancing productivity and safety in environments where manual handling is impractical or unsafe. These systems are built to operate in confined spaces, allowing for precise control over load positioning.
Key Functions:
- Lifting Heavy Materials or Components: Crane systems are engineered to lift substantial weights, making them indispensable in sectors like construction, manufacturing, and logistics. Their lifting mechanisms—such as hoists and trolleys—are designed to handle diverse loads, from small parts to large machinery.
- Moving Loads Horizontally Across Workspaces: The horizontal movement capabilities of crane systems facilitate efficient material handling. This feature is essential in environments like assembly lines and warehouses, where materials need to be transported between different stations or areas without hindrance.
- Lowering Materials Safely to Desired Locations: Safety is paramount in crane operations. Crane systems are equipped with advanced features to ensure that loads are lowered smoothly and accurately, minimizing the risk of accidents or damage. Controls and safety mechanisms work together to provide operators with the ability to lower materials to precise locations without jeopardizing the surrounding environment.
Benefits of Crane Systems:
- Increased Efficiency: By automating the lifting and moving processes, crane systems significantly reduce the time and effort required for manual material handling, leading to enhanced workflow and productivity.
- Improved Safety: With built-in safety features such as overload protection and emergency stop functions, crane systems minimize the risk of accidents, helping to create a safer working environment for employees.
- Versatility in Applications: Crane systems can be tailored for various industries, including construction, manufacturing, automotive, and logistics, allowing for flexible solutions that meet specific operational needs.
- Space Optimization: Designed to operate vertically, crane systems make efficient use of overhead space, freeing up ground-level areas for other operations and improving overall facility layout.
Key Components of Crane Systems
Structural Components Structural components form the backbone of crane systems, providing the necessary framework and stability for safe operation.
- Girder: The main horizontal beam that supports the loa Typically constructed from steel for strength and durability, the girder must be designed to handle the specific weight and dynamics of the materials being lifte
- Runway: Tracks or rails along which the crane operates. Proper installation is crucial to ensure smooth movement and minimize wear over time. Runways must be aligned and leveled accurately to prevent operational issues.
- Supports: Columns or frames that hold the girder and ensure stability. These supports must be anchored securely to the floor or structural elements to withstand load stresses. The design and placement of supports are critical for maintaining structural integrity under various loading conditions.
Mechanical Components Mechanical components are responsible for the actual movement and handling of loads, making them essential for crane functionality.
- Hoist: The mechanism that lifts and lowers loads, available in various types such as electric, manual, or pneumatiHoists often feature safety elements like load limit switches and brakes, which prevent overload and ensure secure handling of materials.
- Trolley: A movable unit that runs along the girder, allowing the hoist to position itself accurately over the loa Trolleys can be powered (motorized) for automated operations or manually operated, depending on the specific application and load requirements.
Electrical Components Electrical components provide the control and power necessary for crane operation, ensuring smooth and safe functionality.
- Control Panel: The interface through which operators manage the crane's functions, including lifting, lowering, and horizontal movement. Modern systems may feature digital displays, joystick controls, and emergency stop functions for enhanced safety and ease of use.
- Motors: These drive the hoist and trolley movements, ensuring reliable operation. Motors may include variable frequency drives (VFDs), which allow for better speed control, increased energy efficiency, and smoother operation during load handling.
By These key components, users can better appreciate how crane systems operate and the importance of each part in ensuring safe and efficient material handling. Proper knowledge of these elements also aids in selecting the right crane system for specific operational needs, enhancing overall productivity and safety in industrial environments.
Subsystems in Crane Operations
Subsystems are integral to the functionality and efficiency of crane operations, comprising various components that work together to ensure safe and effective lifting and movement.
Drive System
The drive system consists of essential components that facilitate the movement of the crane.
- Motors: Provide the necessary power for movement, typically electric but can also be hydraulic or pneumatiThe size and type depend on the crane's capacity and operational requirements, with more powerful motors needed for heavier loads.
- Gears: Convert motor rotation into the desired speed and torque, allowing for precise control of movements. Gear ratios can be adjusted to match specific lifting tasks, ensuring that the crane operates efficiently across various load conditions.
- Chains and Belts: Transfer power from the motors to the hoist and trolley. These components must be regularly inspected for wear and tear to ensure safety and reliability. Proper maintenance is crucial to prevent failures that could lead to accidents.
Control System
The control system is essential for the safe and effective operation of cranes, enabling operators to maneuver loads with precision. Various control options include:
- Cabin Control System: Located within the crane's operator cabin, this system allows for direct operation using joysticks and buttons. It provides a clear view of the working area, enhancing the operator's ability to manage loads effectively. Often equipped with safety features such as emergency stop buttons and load monitoring displays, this system ensures that operators can respond quickly to any issues.
- Remote Control System: Enables operators to control the crane from a distance, increasing safety by allowing them to be away from potential hazards. Wireless technology provides flexibility and ease of movement, making it suitable for complex lifting operations. This system typically includes safety protocols to prevent unintended movements and ensure secure operation.
- Pendant Control System: Utilizes a handheld control unit connected to the crane, allowing operators to maneuver loads while standing at a safe distance. This option offers a balance between manual control and safety, with buttons for lifting, lowering, and moving the trolley. It is often used in applications where operators need to maintain visibility of the load and surrounding are
These control systems helps buyers choose the right option based on their specific operational needs, safety requirements, and the environment in which the crane will be use
Power Supply
The power supply subsystem is vital for providing the energy necessary for crane operation, including options for both powered and manual cranes:
- Wired Systems: Connect directly to the facility's electrical system, delivering continuous power to the crane. These systems are ideal for high-capacity cranes that require a stable energy source for extended operations.
- Battery-Powered Options: Offer flexibility and mobility, especially for portable cranes or in locations where wired connections are impractical. Rechargeable batteries must be regularly monitored for performance to ensure reliable operation, particularly in applications with high deman
- Manual Cranes: Often rely on mechanical systems rather than electrical power, utilizing human effort to lift and move loads. Examples include lever-operated hoists and hand chain blocks, which are cost-effective solutions for lighter loads and smaller spaces. Maintenance for manual cranes involves checking the mechanical components for wear, ensuring safe and effective operation without reliance on electrical systems.
By These power supply options, operators and buyers can make informed decisions based on their specific operational needs and the environment in which the crane will be use This knowledge is crucial for optimizing crane performance and ensuring safe operations.
Types of Overhead Crane Systems
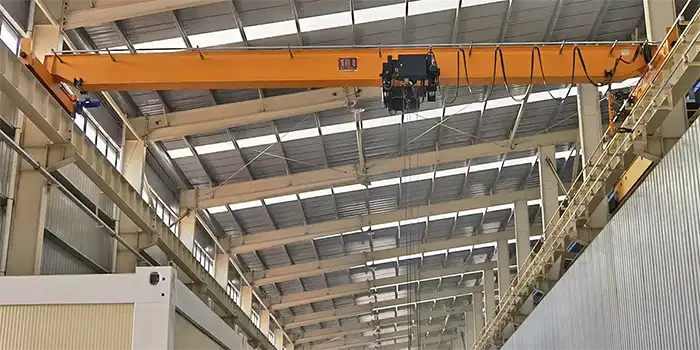
Overhead bridge cranes are essential for lifting and moving heavy loads in various industrial settings. They are designed to enhance operational efficiency while ensuring safety and reliability. Different types of overhead bridge cranes cater to specific applications and load requirements.
Types of Overhead Bridge Crane System:
- Single Girder Bridge Crane System : This crane is designed for lightweight applications and features a single horizontal beam (girder) that supports the hoist. It is cost-effective and ideal for facilities with limited headroom, making it a practical choice for operations where space is a constraint.
- Double Girder Bridge Crane System: Constructed with two parallel beams, the double girder bridge crane provides greater stability and increased load capacity. This type is suitable for heavy-duty tasks and can achieve higher lifting heights, which is essential in environments requiring robust lifting capabilities.
- Top Running Bridge Crane System: Mounted on top of runway rails, top running bridge cranes allow for increased lifting height and capacity. These cranes are commonly used in environments where heavy loads are frequent, such as manufacturing facilities and heavy machinery assembly areas.
- Underhung Bridge Crane System: The underhung bridge crane is suspended from the ceiling, making it perfect for facilities with low overhead clearance. This design offers flexibility in tight spaces while maintaining effective load handling capabilities, ensuring that even constrained environments can benefit from advanced lifting technology.
- Freestanding Bridge Crane System: A self-supporting crane for heavy loads, ideal for spaces without ceiling support, offering efficient material handling.
Typical Features, Applications, and Benefits:
Features:
- High Lifting Capacity: Tailored to specific load requirements, ensuring that operations can handle varying weights effectively.
- Efficient Space Utilization: By freeing up floor areas, these cranes allow for improved workflow and better organization within the workspace.
Applications:Overhead bridge cranes are widely used in manufacturing, warehousing, assembly lines, and maintenance shops. They excel in environments where material handling efficiency is crucial, such as automotive assembly plants and distribution centers.
Benefits:
- Enhanced Safety Features: Including overload protection and limit switches that prevent accidents, ensuring a safer working environment for operators.
- Increased Productivity: By streamlining material movement and reducing reliance on manual labor, overhead bridge cranes contribute to a more efficient and productive operation.
In summary, overhead bridge crane systems are vital tools in optimizing workflow and ensuring the safe handling of materials across various industries, ultimately enhancing overall operational effectiveness.
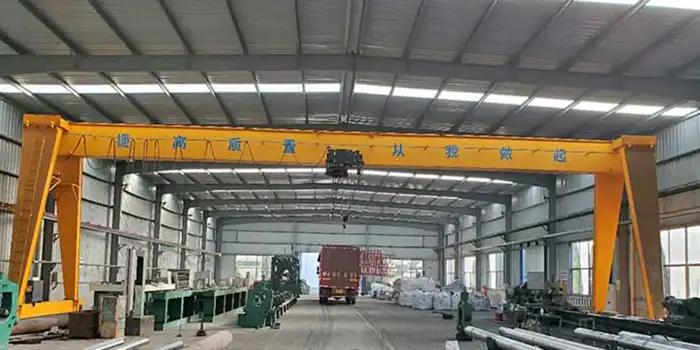
Gantry Crane Systems
Gantry cranes are invaluable in various industries, offering a robust solution for lifting and moving heavy loads. Their design allows for flexibility in operations, making them suitable for diverse applications.
Types og Gantry Crane Systems :
- Full Gantry Crane System: This type consists of a complete framework that can move along rails, providing full mobility for load handling. It is ideal for applications requiring extensive coverage and support for heavy materials, making it a popular choice in environments like shipping yards and large manufacturing plants.
- Semi-Gantry Crane System: The semi-gantry crane features one side on wheels while the other is fixed, allowing for partial movement along a designated path. This design is particularly suitable for areas where space is limited but some mobility is still required, enabling efficient handling without sacrificing stability.
- Portable Gantry Crane System: Lightweight and designed for easy relocation, portable gantry cranes are perfect for temporary job sites. They offer convenience for tasks that require flexibility and quick setup, making them ideal for maintenance operations and small-scale construction projects.
Typical Features, Applications, and Benefits:
Features:
- Versatility: Highly versatile, capable of lifting and moving heavy loads across various terrains.
- Customizable Hoisting Mechanisms: Can be equipped with different hoisting mechanisms to suit specific operational needs, enhancing functionality.
Applications:
- Gantry cranes are commonly used in shipping yards, outdoor construction sites, and manufacturing facilities. They are effective for tasks such as loading and unloading materials, assembly, and equipment maintenance, making them essential in many workflows.
Benefits:
- Operational Flexibility: Provides flexibility in operations, allowing for quick adjustments based on job requirements, which is crucial for dynamic work environments.
- Ease of Use: Easy to maneuver and operate, reducing the need for extensive operator training and enhancing safety.
In conclusion, gantry crane systems offer a blend of mobility, versatility, and efficiency, making them a preferred choice in numerous industries for effective material handling.
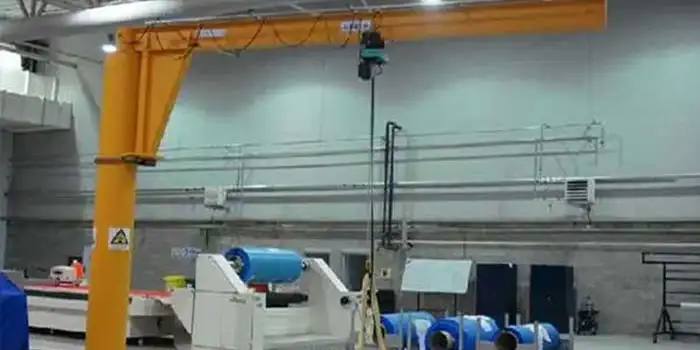
Jib Crane Systems
Jib cranes are essential for lifting and positioning tasks in confined spaces, providing efficiency and flexibility in various operational settings. Their design allows for effective load handling while maximizing the use of available space.
Types of Jib Crane Systems:
- Wall-Mounted Jib Crane System: These cranes are secured to a wall, saving valuable floor space while enabling efficient lifting within a confined are They are ideal for light to moderate loads, making them particularly suitable for workshops and assembly lines where space is at a premium.
- Freestanding Jib Crane System: As independent structures, freestanding jib cranes can be positioned anywhere within a facility, offering flexibility in load handling. They are excellent for environments that allow for movement and require a dedicated lifting solution, providing operators with more options.
- Articulating Jib Crane System: Featuring flexible arms that can extend and rotate, articulating jib cranes provide greater reach and versatility for maneuvering loads. This type is best suited for areas with obstacles or where precise positioning is necessary, allowing operators to navigate tight spaces effectively.
Recognizing the diverse types of jib cranes helps in The their specific features, applications, and benefits, which are crucial for enhancing operational efficiency.
Typical Features, Applications, and Benefits:
Features:
- Rotating Arms: Equipped with rotating arms that allow for 360-degree movement, optimizing load handling and positioning.
- Compact Design: The compact design minimizes the footprint while maximizing functionality, making them ideal for limited spaces.
Applications:
- Jib cranes are commonly used in workshops, small manufacturing areas, and maintenance shops for lifting and positioning tasks. They excel in applications that require precise handling of materials in tight spaces, improving workflow efficiency.
Benefits:
- Enhanced Maneuverability: Jib cranes enhance maneuverability, enabling operators to lift and move loads easily within restricted areas, thus improving productivity.
- Improved Access: Providing easy access to loads reduces the risk of accidents and enhances overall operational efficiency, making them a valuable asset in any workspace.
In summary, jib crane systems play a pivotal role in facilitating safe and efficient material handling, particularly in environments where space is limited and precision is key.
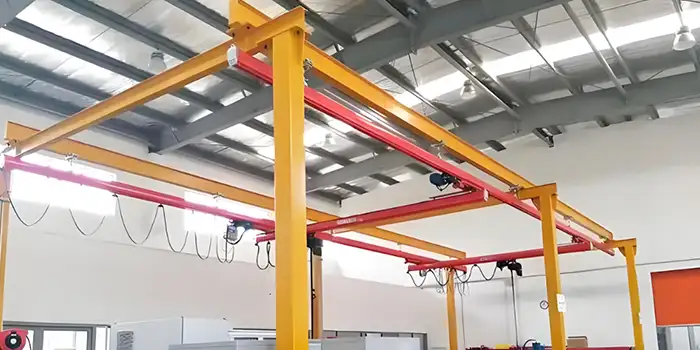
KBK Rail Systems
KBK rail systems are versatile solutions designed for efficient material handling across various industrial applications. Their modular design and adaptability make them suitable for different operational needs, enhancing productivity and safety.
Types of KBK Crane Systems:
- Single Track Kbk Crane System: This system is ideal for simpler setups and lighter applications, where space and budget constraints are factors. It provides efficient movement along a designated path, making it suitable for smaller facilities or specific tasks that require precise handling.
- Double Track Kbk Crane System: Offering greater support for heavier loads, double track systems accommodate more complex operations and increased lifting capabilities. They allow for the simultaneous movement of multiple trolleys, which enhances productivity in larger workspaces, making them ideal for busy production environments.
- Curved and Straight Kbk Crane System: Flexible configurations are a hallmark of KBK rail systems. Curved tracks enable navigation around obstacles, while straight tracks facilitate straightforward material transport, allowing for tailored solutions that adapt to various facility layouts.
Recognizing the types of KBK rail systems sets the stage for The their typical features, applications, and benefits, which are critical for maximizing operational efficiency.
Typical Features, Applications, and Benefits:
Features:
- Modular Design: The modularity of KBK systems allows for easy customization and expansion based on operational needs, enabling facilities to adapt to changing requirements without significant investment.
- Smooth Operation: These systems are designed for minimal friction, leading to smooth operation and reduced wear and tear on components, which can extend the lifespan of the equipment.
Applications:
- KBK rail systems are commonly used in assembly lines, warehouses, and production areas for efficient load handling. They find applications across various industries, including automotive, aerospace, and manufacturing, where efficient material transport is essential.
Benefits:
- Operational Flexibility: The ability to customize configurations enhances operational flexibility, allowing for tailored solutions that fit specific workflows and processes.
- Enhanced Safety and Efficiency: By improving material handling practices, KBK rail systems contribute to overall productivity while enhancing safety within the workplace.
In summary, KBK rail systems offer a robust solution for diverse material handling challenges, making them an excellent choice for industries seeking to improve efficiency and safety in their operations.
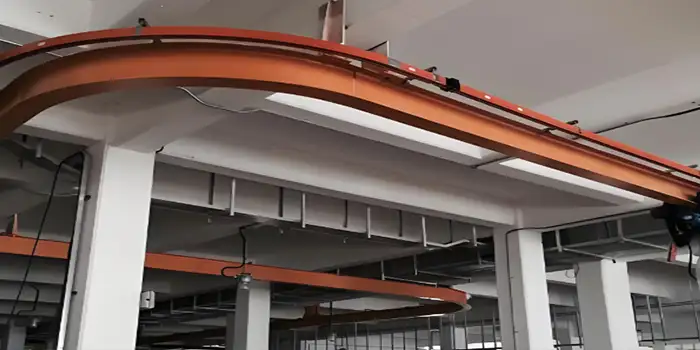
Monorail Crane Systems
Monorail crane systems provide efficient solutions for lifting and transporting materials in various industrial settings. Their design allows for streamlined operations, particularly in environments where space is a consideration.
- Single Monorail Crane System:A simple track system for lightweight loads, ideal for limited spaces, allowing smooth movement along a straight path to enhance productivity.
- Curved Monorail Crane System:Designed for non-linear layouts, this system enables smooth movement around curves, improving material handling flexibility in complex environments.
- Floor-Mounted Monorail Crane System:A stable, ground-based track system for areas with limited overhead space, providing precise material movement along a fixed path.
Typical Features, Applications, and Benefits:
Features:
- Streamlined Movement: Monorail systems provide streamlined movement that enhances operational flow, effectively reducing the likelihood of bottlenecks.
- Space-Saving Design: Their design utilizes overhead space efficiently, keeping floors clear for other activities, which is crucial in busy environments.
Applications:
- Monorail crane systems are widely used in assembly lines and warehouse logistics for efficient material transport. They are particularly beneficial in manufacturing facilities where quick load handling is crucial for maintaining workflow.
Benefits:
- Increased Efficiency: By minimizing the time spent on load handling and transportation, monorail systems significantly increase operational efficiency.
- Reduced Handling Times: These systems lead to smoother operations and higher productivity rates by reducing overall handling times, allowing facilities to operate more effectively.
In summary, monorail crane systems are a vital component in optimizing material handling processes, particularly in spaces where efficiency and effective use of overhead space are critical.
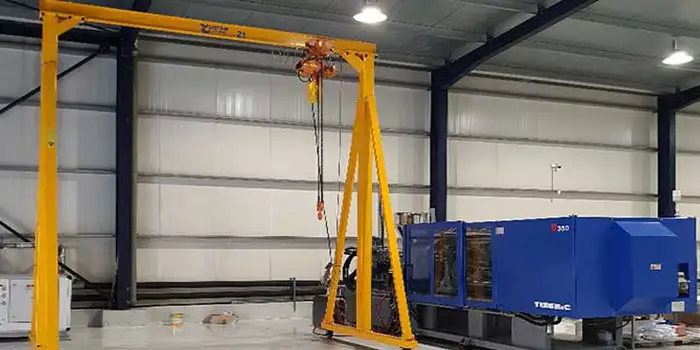
Portable Crane Systems
Portable crane systems are designed for versatility and ease of use, making them ideal for a range of applications where mobility and quick setup are essential. These cranes provide effective solutions for lifting tasks in various environments, ensuring operational efficiency without compromising safety.
Types of Portable Crane Systems:
- A-Frame Portable Gantry Cranes : The A-frame crane features a stable, triangular design that provides excellent support in diverse environments. This type is suitable for various lifting tasks and can accommodate different load sizes, making it adaptable for numerous applications.
- Foldable Gantry Gantry Crane System : Designed for easy transportation and storage, the foldable gantry crane can collapse for compactness. This type is ideal for scenarios where space is limited or when the crane needs to be relocated frequently, providing convenience without sacrificing functionality.
- Portable Jib Crane System :A mobile, flexible crane for lifting light to moderate loads. Ideal for quick setup in workshops, warehouses, or outdoor sites.
Transitioning from The the types of portable crane systems, it's crucial to delve into their typical features, applications, and benefits to grasp their full impact on operational efficiency.
Typical Features, Applications, and Benefits:
Features:
- Lightweight Construction: Portable cranes are built with lightweight materials, allowing for easy handling and maneuverability, which is vital in dynamic work environments.
- Quick Assembly and Disassembly: These cranes can be set up and taken down rapidly, enabling users to move efficiently between different locations and tasks.
Applications:
- Portable crane systems are commonly used in maintenance tasks, such as equipment servicing or repairs, where quick access and flexibility are require
- They are also ideal for temporary setups in construction sites, workshops, or event staging, accommodating various lifting needs with minimal setup time.
Benefits:
- High Mobility: The design of portable cranes allows users to transport them easily, increasing operational flexibility and enabling them to adapt to changing job requirements.
- Convenience for On-the-Go Applications: These systems reduce downtime by providing quick solutions for lifting and moving loads, ultimately enhancing productivity and ensuring tasks are completed efficiently.
In summary, portable crane systems are invaluable tools in settings where mobility and adaptability are paramount, helping to streamline operations across multiple industries.
Key Considerations for Crane Buyers
When selecting a crane, there are several critical factors to consider that can significantly impact operational efficiency, safety, and overall investment. By carefully evaluating these elements, buyers can ensure they choose the right system for their needs.
Load Capacity and Specifications The load capacity is essential for safe and efficient crane operation. Buyers should assess the following:
- Maximum Load: Determine the heaviest load the crane will handle to ensure it meets operational demands.
- Working Load Limit (WLL): This specification is crucial for maintaining safety during lifting operations.
- Dynamic vs. Static Loads: Consider both types of loads, as dynamic loads may require additional safety factors to prevent accidents.
Transitioning from load specifications, it's important to examine the workspace and installation requirements to maximize crane performance.
Workspace and Installation Requirements Evaluating the facility layout is critical for optimal crane performance:
- Headroom: Measure the vertical space to ensure the crane can operate without obstruction.
- Footprint: Analyze the available floor space to accommodate the crane and its movement effectively.
- Access Points: Ensure there are adequate access routes for crane operation and maintenance, which is vital for efficiency.
As we consider installation, safety features and compliance standards also play a vital role in crane selection.
Safety Features and Compliance Standards Compliance with industry safety standards is non-negotiable for crane operations:
- Overload Protection: This essential feature prevents lifting loads beyond the crane's capacity, enhancing safety.
- Emergency Stops: Critical for halting operations immediately in case of an emergency, ensuring worker safety.
- Compliance: Ensure the crane adheres to OSHA, ANSI, and other relevant regulations to meet industry standards.
In addition to safety, ongoing maintenance and service considerations are vital for long-term operation.
Maintenance and Service Considerations Regular maintenance is crucial for safe and efficient operation:
- Service Support: Consider suppliers that offer reliable maintenance services and support to ensure timely assistance.
- Replacement Parts: Ensure easy access to spare parts to minimize downtime and maintain productivity.
- Maintenance Schedule: Establish a routine maintenance plan to prolong the crane's lifespan and prevent unexpected failures.
Finally, evaluating costs and budget constraints will help buyers make informed financial decisions.
Cost and Budget Constraints Assessing the total cost is vital for staying within budget:
- Initial Purchase Price: Factor in the cost of the crane and any custom features that may be necessary for specific applications.
- Installation Costs: Include expenses for professional setup and any facility modifications needed to accommodate the crane.
- Ongoing Maintenance: Consider regular maintenance and inspection costs as part of total ownership expenses to ensure long-term viability.
- Long-Term Investment: Evaluate the crane's potential to enhance productivity and reduce operational costs over time, ensuring a sound financial decision.
By taking these key considerations into account, buyers can make well-informed choices that align with their operational needs and budgetary constraints.Contact us to get your customized overhead crane system for your material handling. Conact us today to chec what we can do to save your crane cost.