32/5 Ton Overhead Crane Sale in India: Case Study
Overview of the Crane for Sale
Description: 32/5 Ton Overhead Crane
The 32/5 Ton Overhead Crane is designed to handle heavy-duty lifting operations, making it an ideal choice for industries that require robust and reliable equipment. This model offers a combination of power, efficiency, and safety, ensuring it meets the high demands of industrial environments.
Type: Traditional Overhead Open Winch Crane
This crane is a traditional overhead open winch crane, which is a widely recognized and reliable crane type in various industrial applications. The open winch design offers advantages in terms of ease of maintenance, reliability, and efficiency in operation. This crane type is well-suited for handling heavy loads in a range of manufacturing and construction environments, where precision lifting and durability are critical.
Features: Heavy Duty, High Safety, Affordable
- Heavy Duty: The 32/5 Ton Overhead Crane is designed for high load capacities and intensive operations, capable of lifting up to 32 tons at a time. Its heavy-duty design ensures that it can handle large, cumbersome materials and equipment with ease, making it suitable for industries such as steel manufacturing, automotive, and construction.
- High Safety: Safety is a top priority for this crane model. It comes equipped with safety features such as emergency stop functions, overload protection, and limit switches, ensuring that the crane operates within safe parameters. These safety measures protect workers and equipment from accidents and damage.
- Affordable: Despite its heavy-duty capabilities, the crane is cost-effective, making it an attractive option for businesses looking to invest in quality equipment without exceeding their budget. Its competitive pricing does not compromise its performance or safety, making it an ideal choice for companies that require high-performance cranes at a reasonable cost.
Purpose: Industrial Applications Requiring High Performance and Reliability
The 32/5 Ton Overhead Crane is intended for industrial applications that demand both high performance and reliability. It is particularly useful in:
- Manufacturing: Ideal for factories and production lines where materials need to be moved efficiently and safely between different stages of production.
- Heavy-Duty Lifting: This crane is well-suited for environments where large, heavy items such as steel, machinery, or construction materials need to be lifted or positioned with precision.
- Warehouse Operations: Used in storage facilities for organizing, loading, and unloading heavy goods and equipment.
In summary, this crane is built to provide maximum reliability and efficiency in challenging industrial settings, ensuring that operations run smoothly without compromising on safety or cost-effectiveness.
Importance of Crane Specifications
The specifications of a crane are crucial in determining its suitability for various applications, ensuring it can handle the required loads, reach the necessary lifting heights, and operate efficiently. In this section, we will break down the QD model configurations of the 32/5 Ton Overhead Crane, along with the electrical specifications, highlighting their importance for industrial applications.
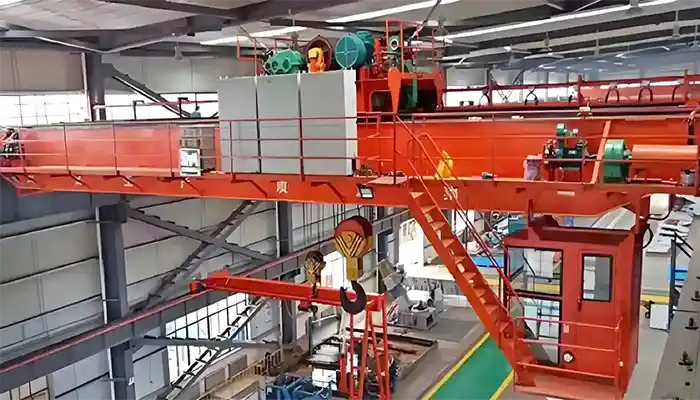
Double girder overhead crane with open trolley for your reference
QD Model Configurations
The QD (Double Girder) Model configurations for the 32/5 Ton Overhead Crane are carefully designed to cater to different operational needs, providing flexibility in lifting capacities, spans, and lifting heights. Here are the key configurations:
32/5T-13.5M H27/27.8M
- Load Capacity: 32 tons (Main Hook) and 5 tons (Auxiliary Hook)
- Span (M): 13.5 meters
- Lifting Height (H): 27 meters (Main Hook), 27.8 meters (Auxiliary Hook)
- This configuration is suited for heavy-duty operations requiring high lifting heights and the ability to handle large materials.
32/5T-13.5M H16/16.8M
- Load Capacity: 32 tons (Main Hook) and 5 tons (Auxiliary Hook)
- Span (M): 13.5 meters
- Lifting Height (H): 16 meters (Main Hook), 16.8 meters (Auxiliary Hook)
- Ideal for operations where moderate lifting height is needed with a strong load capacity.
32/5T-16M H22/22.8M
- Load Capacity: 32 tons (Main Hook) and 5 tons (Auxiliary Hook)
- Span (M): 16 meters
- Lifting Height (H): 22 meters (Main Hook), 22.8 meters (Auxiliary Hook)
- This configuration is perfect for operations requiring both a wider span and considerable lifting height.
10T-13.5M H27M
- Load Capacity: 10 tons (Main Hook)
- Span (M): 13.5 meters
- Lifting Height (H): 27 meters
- A more specialized configuration for lighter loads but still offering considerable height and span.
16T-15.5M H14M
- Load Capacity: 16 tons (Main Hook)
- Span (M): 15.5 meters
- Lifting Height (H): 14 meters
- This configuration is designed for medium-heavy lifting operations with moderate height and span.
32/5T-18.5M H20/20.8M
- Load Capacity: 32 tons (Main Hook) and 5 tons (Auxiliary Hook)
- Span (M): 18.5 meters
- Lifting Height (H): 20 meters (Main Hook), 20.8 meters (Auxiliary Hook)
- Ideal for large-scale industrial operations that require significant reach and lifting height, such as heavy manufacturing.
single girder overhead cranes
Voltage: 415V 50HZ 3P
The crane is designed to operate with a 415V 50HZ 3-phase electrical system, which is commonly used for industrial equipment across many regions, ensuring compatibility with global standards. Here’s why the voltage specification is important:
- Robust Performance: This voltage level ensures that the crane operates smoothly under heavy loads without compromising performance. It helps in powering the crane's motors, winches, and other electrical components efficiently.
- Global Standard: The 415V 50HZ 3-phase configuration is widely used in various industries around the world, allowing for easy integration into international projects and ensuring that the crane can operate in multiple regions without requiring significant adjustments to the electrical system.
- Energy Efficiency: The 3-phase electrical system offers better energy efficiency compared to single-phase systems, leading to lower operational costs and increased durability of the crane's electrical components.
Why These Specifications Matter
The QD model configurations ensure that the crane can be tailored to the specific needs of different industrial applications, whether it's for heavy manufacturing, warehousing, or construction. The crane's ability to handle varying load capacities and reach specific heights gives buyers flexibility in their operations.
The 415V 50HZ 3-phase electrical system ensures the crane performs reliably, aligns with international electrical standards, and can be used in diverse industrial environments, improving the overall efficiency of operations.
In summary, these specifications are not just numbers—they are key factors that determine the crane's efficiency, safety, and suitability for different types of industrial tasks. Having a clear understanding of these specifications helps buyers make informed decisions based on their unique lifting requirements and operational conditions.
Main girder of overhead crane for sale India
Main girder of overhead crane for sale India
Main girder of overhead crane for sale India
Main girder of 32 ton overhead crane for sale India
end carriage of overhead crane for India
end trucks or end carriages of overhead bridge cranes
Open winch trolley for you the double girder open winch trolley
end carriages of overhead bridge crane
main parts of 32 /5 ton overhead crane
main parts of electric overhead travelling crane
main parts and components of double girder overhead crane with open winch trolley for sale India
Production Timeline and Key Milestones
The production of the 32/5 Ton Overhead Crane follows a carefully planned timeline, with various milestones marking significant progress throughout the assembly process. Below is a detailed breakdown of the key milestones and events leading to the crane's completion.
6.27: Factory Order Placed
- Event: Official order placed for 4 sets of cranes.
- Details: Initial planning phase begins. Resource allocation, such as procurement of materials, allocation of labor, and machinery setup, starts to prepare for the assembly process.
- Impact: The placement of the factory order initiates the production schedule and establishes timelines for the completion of all necessary crane components.
8.12: Beam Box Completed, End Beams in Production
- Event: Completion of the beam box, with end beams currently in production.
- Details: The beam box is a critical structural element of the crane, marking an important stage in the assembly. The end beams are essential to the crane's structural integrity, supporting the lifting mechanisms and ensuring stability during operation.
- Impact: The completion of the beam box signifies that key structural components are on track, while the production of end beams indicates progress towards completing the frame of the crane.
8.20: Single Girder Crane End Beams Painted, Motor Installation Pending
- Event: The end beams for the single girder crane are painted, with motor installation still pending.
- Details: Painting of the end beams indicates that the structural assembly is almost complete for the single girder crane. The motor installation is a crucial next step that will bring the crane’s lifting mechanism into operation.
- Impact: The progress on the single girder crane shows the assembly nearing the final stages, but the motor installation delay shows that the crane is not yet fully operational.
8.22: QD Crane Production Paused, LC Delayed by 4-6 Months
- Event: Production pause for the QD crane due to Letter of Credit (LC) delay.
- Details: The production of the QD (double girder) crane halts as a result of a 4-6 month delay in payment due to the LC. The delay of the LC, a common form of international payment, prevents the manufacturer from securing the necessary funds to proceed with production.
- Impact: The delay in payment causes a significant pause in the production schedule, disrupting timelines for delivery and assembly. The lack of immediate payment is one of the primary causes of production halts, highlighting the importance of timely financial arrangements.
Double Girder Crane: Wheel Assembly Started
- Event: Wheel assembly for the double girder crane has begun.
- Details: As part of the double girder crane assembly, the wheels are crucial for mobility, enabling the crane to move along its tracks. The assembly of the wheels is a vital step in ensuring that the crane can operate smoothly.
- Impact: The wheel assembly process indicates steady progress on the double girder crane. Once the wheels are fully assembled, they will enable the crane’s movement and contribute to the crane’s overall functionality.
Grab Bucket: Formed, Trolley Material Cutting in Progress
- Event: Grab bucket is formed, with trolley material cutting in progress.
- Details: The grab bucket, used for material handling, has been shaped and is ready for the next stages of production. At the same time, the material for the trolley is being cut, which is a critical part of the crane’s lifting mechanism.
- Impact: This marks important progress in the crane’s lifting system. Once the trolley material is fully prepared, it will be assembled and integrated into the crane, making it capable of lifting and moving loads efficiently.
Drum, Wheels, Motor, and Gearbox Expected to be Completed or Delivered
- Event: Completion of critical components—drums, wheels, motor, and gearbox—expected this week.
- Details: The drums, wheels, motor, and gearbox are essential mechanical components that ensure the crane operates effectively. The expected completion and delivery of these parts are vital for moving into the final assembly phase of the crane.
- Impact: The timely delivery of these components is crucial for keeping the production timeline on track. Once received, assembly will progress swiftly towards final completion, allowing for testing and commissioning.
This production timeline showcases the various stages and challenges faced during the assembly of the 32/5 Ton Overhead Crane. Key milestones, such as the completion of major structural components, progress in assembly, and the interruption caused by the delayed LC, demonstrate the importance of each stage in the overall crane manufacturing process. Ensuring timely payments, managing component delivery, and addressing production delays effectively are crucial for meeting customer expectations and delivery schedules.
Analysis of Payment Delays and Production Impact
The 32/5 Ton Overhead Crane manufacturing process has been significantly impacted by the 4-6 month delay in the Letter of Credit (LC) payment. This delay caused disruptions in multiple areas of the production schedule and affected supplier relationships, customer satisfaction, and cash flow. Below is a breakdown of how the payment delay affected the production process.
Effect of LC Delay on Production Schedule
The LC payment delay resulted in a major halt in production. Without the necessary funds, the manufacturer was unable to proceed with procurement, labor allocation, or parts assembly.
Production Halt: The delay meant that key components such as motors and gearboxes could not be procured, and the assembly of the crane could not continue as planned.
- The lack of timely funds caused a complete stop in the production process.
- Crucial tasks like motor installation and gearbox assembly were postponed.
Impact on Timelines:
- The production schedule was delayed, meaning the expected delivery of the cranes would be late.
- The pause in production led to potential missed deadlines, which is especially critical in industries with tight timeframes.
Disrupted Cash Flow
A delay in receiving payment through the LC caused a significant disruption to the manufacturer’s cash flow.
Financial Strain:
Without the incoming funds, the factory could not pay for critical components or operational costs. This led to a freeze on material purchases and labor allocation.
- Inability to pay suppliers or cover labor costs directly affected production.
- The delay created a backlog of operational requirements and slowed down progress.
Impact on Operations:
- The financial disruption halted procurement of essential parts, leading to extended lead times and a general slowdown in the manufacturing process.
- It underscored the reliance on prompt payments in large-scale industrial production.
Consequences for Crane Assembly
The delay in LC payment had direct consequences on the availability of essential parts, such as motors and gearboxes, which are crucial for crane assembly.
Parts Availability:
- Critical components like motors, gearboxes, and mechanical parts were delayed due to the lack of funds for supplier payments.
- Without these key parts, assembly could not proceed, and the production timeline was pushed back.
Impact on Production:
- The inability to secure these parts meant that assembly could not continue as scheduled, delaying the overall manufacturing process.
- As a result, the project faced major setbacks, leading to extended lead times and potential cost increases.
Customer Impact
The delays in production due to the LC payment delay had a direct effect on the delivery timelines for customers.
Late Deliveries:
- The crane’s late production and assembly caused a delay in delivery to customers.
- Delays in delivering the cranes affected customers' own project schedules and operations.
Customer Satisfaction:
- Delayed delivery leads to decreased customer satisfaction, as clients may need to adjust their timelines or operations to accommodate the delay.
- The risk of losing customer trust increases, which may affect the manufacturer's reputation and future business opportunities.
Impact on Supplier Relationships
The delayed LC payment also strained the manufacturer’s relationships with its suppliers.
Strained Trust and Collaboration:
- Suppliers were hesitant to continue supplying parts on credit, fearing further payment delays.
- Uncertainty regarding future payments can cause suppliers to raise prices or even cease business dealings with the manufacturer.
Impact on Future Transactions:
- Ongoing delays can break down trust between the manufacturer and suppliers, making it harder to secure favorable payment terms in the future.
- Suppliers may begin to demand stricter payment terms or refuse to extend credit, which can increase costs and complicate future transactions.
Long-Term Supplier Relations
The long-term effects of delayed payments can have serious consequences on future supplier relationships.
Stricter Payment Terms:
- Suppliers may require upfront payments or shorter credit terms to mitigate the risk of further delayed payments.
Increased Costs and Complicated Deals:
- Tighter payment terms can lead to higher operational costs.
- The manufacturer may find it more difficult to negotiate favorable terms in future purchases, leading to increased expenses and reduced flexibility in sourcing materials.
The 4-6 month LC payment delay has had far-reaching impacts on the production, supplier relationships, and customer satisfaction regarding the 32/5 Ton Overhead Crane. The production schedule was disrupted, key components were delayed, and the crane’s delivery was postponed.
This case highlights the importance of timely payments in crane manufacturing. To avoid similar issues, manufacturers should work closely with their buyers and financial institutions to ensure that payments are processed efficiently and promptly. By doing so, manufacturers can protect their production schedules, maintain healthy supplier relationships, and keep customer satisfaction intact.
Mitigation Strategies for Payment Delays in Crane Manufacturing
Payment delays in crane manufacturing can significantly disrupt production schedules, strain supplier relationships, and negatively affect customer satisfaction. To mitigate these risks, manufacturers must implement strategies that minimize delays and ensure smoother operations. Below are key approaches that can help keep production on track:
Timely Issuance of Letters of Credit (LC)
Importance of Timely LC Issuance:
The timely issuance of a Letter of Credit (LC) is one of the most effective ways to avoid payment delays. A properly issued LC serves as a guaranteed payment method, offering both the buyer and the seller the confidence to proceed with production and procurement.
- Actionable Tip:
Ensure that the LC is issued well in advance of the scheduled production start date. Set clear deadlines with the buyer for when the LC should be issued and ensure both parties understand the necessary documentation and procedures.
Clear Communication with Buyers:
Payment delays often arise from miscommunications regarding payment timelines. Therefore, maintaining regular and transparent communication with the buyer about payment expectations is essential.
- Actionable Tip:
Set expectations early regarding the LC’s processing time and ensure both parties agree on how long it will take for payments to be processed.
Proactive Monitoring of LC Status
Constant Follow-Up:
Once the LC is issued, continuous monitoring of its status is critical to ensure its confirmation and timely processing. Regular follow-ups with both the buyer and the bank help to identify any potential delays early.
- Actionable Tip:
Establish a system to track the LC’s progress and set reminders for regular checks. If any issues arise, address them promptly to avoid production interruptions.
Avoiding Last-Minute Issues:
Checking the LC status well before the production timeline ensures that any issues can be resolved in advance. Proactive monitoring prevents last-minute delays that could halt production.
- Actionable Tip:
Aim to have the LC confirmed at least two weeks before production starts. This will allow enough time to handle any discrepancies or problems that may arise.
Using Partial Payments
Implementing Progress or Milestone Payments:
One effective strategy to ensure consistent cash flow during production is to negotiate progress or milestone-based payments. With partial payments, manufacturers can receive payments incrementally as specific production stages are completed, reducing the need to wait for full payment at the end.
- Actionable Tip:
Negotiate a payment schedule linked to clear milestones, such as beam fabrication completion, assembly of key components, or installation of the crane's motor. This ensures that funds are available when needed for ongoing production.
Advancing Payments for Critical Components:
Critical parts such as motors, gearboxes, and steel components can cause delays if not procured on time. Securing advance payments for these high-cost components helps ensure their timely delivery, preventing disruptions in the assembly process.
- Actionable Tip:
Agree with the buyer to make advance payments for essential components before their procurement. This allows the manufacturer to order parts early and avoid delays in receiving key materials.
Contingency Plans for Delayed Payments
Setting Up Alternate Financing Arrangements:
To mitigate the impact of unexpected payment delays, manufacturers should establish backup financing options. These can include bank guarantees, standby LCs, or other credit facilities to keep production moving forward even if the primary payment is delayed.
- Actionable Tip:
Discuss potential backup financing arrangements with the buyer and financial institutions at the outset. Options like bank guarantees or short-term loans can provide an extra layer of security in case of delays.
Using Standby LCs:
A standby LC can serve as a safeguard in case the primary LC is delayed or fails to cover the full amount. This financial backup provides security and ensures that production can continue without interruption.
- Actionable Tip:
Consider negotiating a standby LC alongside the primary LC. This ensures that sufficient funds are available in case of any issues with the main payment.
Mitigating payment delays is critical for maintaining smooth operations in crane manufacturing. By adopting strategies like ensuring the timely issuance of LCs, monitoring the LC status proactively, implementing partial payments, and establishing contingency plans, manufacturers can avoid production disruptions and ensure timely deliveries. These strategies not only help maintain cash flow but also foster stronger, more reliable relationships with both suppliers and buyers, leading to more efficient and predictable project execution.
Conclusion
The delay in the Letter of Credit (LC) payment has caused significant disruptions to crane production. The production process has been halted for up to 4-6 months, with parts like motors, gearboxes, and other critical components delayed, which, in turn, has led to a cascading effect on the assembly and delivery timelines. These delays have impacted both the crane manufacturing process and the overall project deadlines, potentially harming customer satisfaction and future business prospects.
Timely payments are critical to the success of crane manufacturing. Smooth financial transactions ensure that the necessary materials, parts, and labor are available when required, preventing production delays. For crane manufacturers, receiving payments on time means they can maintain a steady cash flow, meet production deadlines, and sustain positive relationships with suppliers. Without this, the risk of operational disruptions increases, potentially resulting in significant financial losses and damage to business reputations.
Recommendations for Buyers and Sellers
- For Buyers: Buyers should collaborate closely with their banks to ensure that Letters of Credit (LCs) are processed promptly and without discrepancies. Timely issuance and confirmation of LCs will help avoid delays that disrupt the manufacturing process.
- For Sellers: Sellers must ensure that contracts clearly define payment timelines, the LC issuance process, and the consequences of delayed payments. Clear terms in the agreement will set expectations upfront, reducing the likelihood of payment delays and their subsequent impact on production.
By following these best practices, both buyers and sellers can mitigate the risks of payment delays, ensuring the successful and timely delivery of crane orders.
Article by Bella ,who has been in the hoist and crane field since 2016. Bella provides overhead crane & gantry crane consultation services for clients who need a customized overhead travelling crane solution.Contact her to get free consultation.