Choosing Right Rail-Mounted Gantry Crane for Intermodal Operations
Choosing the Right Rail-Mounted Gantry Crane for Intermodal Operations
What are Intermodal Rail Yards?
Intermodal rail yards are busy hubs where containers are transferred between different types of transport, like trains, trucks, and storage areas. These yards are crucial for moving goods efficiently, connecting rail and road transportation to speed up deliveries. Since these yards are central to the entire supply chain, they rely on equipment that can handle a steady flow of containers without slowing down.
One of the most important pieces of equipment in these yards is the Rail-Mounted Gantry (RMG) crane. It’s responsible for lifting containers off trains and placing them onto trucks or into storage. To keep things running smoothly, the crane has to work quickly, safely, and reliably.
Why the Right Crane is So Important
Picking the right RMG crane is key to making sure everything runs efficiently. If you choose the wrong crane, it can slow things down, cause safety problems, and end up costing more. A crane that’s designed for the specific needs of the yard will help boost efficiency, reduce delays, and make sure containers keep moving.
The crane needs to fit the type of containers being moved, the size of the yard, and the speed of operations. Plus, it should be able to handle whatever environmental challenges the yard faces, like weather or space constraints.
How RMG Cranes Help Move Containers
RMG cranes are built for transferring containers between railcars, trucks, and storage. They run on rails, which lets them move up and down the yard’s tracks and reach containers wherever they’re needed.
- Faster Container Handling: RMG cranes can quickly and accurately pick up heavy containers, which speeds up the transfer process and reduces wait times for trains, trucks, and storage.
- Flexibility and Reach: These cranes can cover a large area, moving across multiple railcars or truck lanes at once. This means the yard can make the most of its space and handle more containers.
By ensuring containers are moved quickly and accurately, RMG cranes help keep the entire yard running smoothly. Their ability to work efficiently in busy environments makes them essential for intermodal rail yards.
Rail-Mounted Gantry (RMG) Cranes
What Are RMG Cranes and What Makes Them Special?
Rail-Mounted Gantry (RMG) cranes are big machines designed to move containers around busy intermodal yards. They're called "rail-mounted" because they run on tracks, just like a train, and they’re built to lift and transfer containers from railcars to trucks or storage areas.
Key Features of RMG Cranes:
- Rail Tracks: These cranes move along tracks, giving them the ability to cover large distances within the yard.
- Heavy Lifting: RMG cranes are built to handle large, heavy containers, making them essential for busy ports and rail yards.
- High Reach: They can lift containers to great heights, which helps when stacking or placing containers on higher storage areas.
RMG cranes are particularly well-suited for intermodal yards because they can move containers quickly and efficiently between different types of transport. They are the perfect solution when you need to switch containers between trains, trucks, and storage areas.
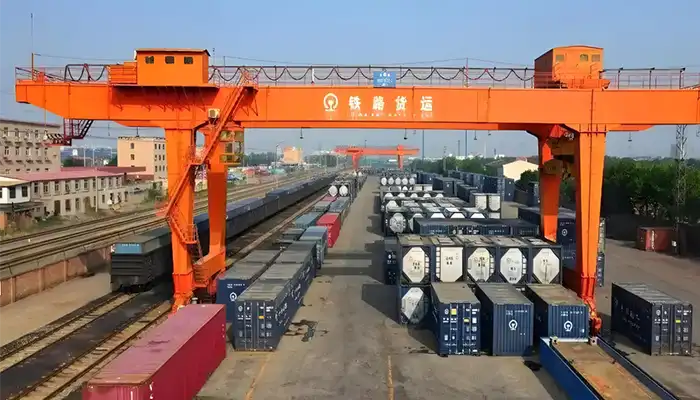
rail mounted gantry crane for railroad container handling
How Are RMG Cranes Different from Other Cranes?
RMG cranes stand out from other cranes like rubber-tyred gantry (RTG) cranes because of their design and operation.
- RMG vs. RTG: While RTGs run on rubber tires and are more flexible in terms of movement, RMGs are fixed to rail tracks. This gives RMGs more stability and higher capacity for handling heavy containers.
- Space Efficiency: Because they are fixed on rails, RMGs can be designed to work in tighter, more organized spaces, helping to optimize yard layout and container stacking.
In simple terms, RMG cranes are better suited for areas where high lifting capacity and stability are needed, especially in rail yards that handle large volumes of containers.
How RMG Cranes Help with Intermodal Transfers
RMG cranes play a key role in the smooth running of intermodal yards. They transfer containers from railcars to trucks or storage, making them essential for the flow of goods.
- Efficient Container Movement: RMG cranes quickly pick up containers from trains and place them onto trucks or storage areas without delays. This speeds up the process of moving goods in and out of the yard.
- Versatility: RMG cranes can handle all types of cargo, whether it’s heavy, large, or oddly shaped. Their adjustable features make them ideal for different container types.
- Optimizing Yard Space: These cranes are designed to work efficiently within a limited area, allowing yards to store more containers without taking up too much space. By covering long distances and reaching across multiple rows of containers, RMG cranes help maximize the use of available yard space.
In short, RMG cranes are the backbone of intermodal rail yards, helping to ensure that containers are moved quickly, safely, and efficiently.
Key Considerations for Choosing an RMG Crane
Operational Requirements
When selecting an RMG crane, it’s important to think about the specific needs of the rail yard. This includes defining the crane’s capacity based on the loads it will carry and the types of containers it will handle.
- Crane Capacity: The crane must be able to lift containers of various weights without straining. This means considering not only the average load but also the maximum weight of containers expected in the yard.
- Lifting Height and Span: The crane needs to reach high enough to stack containers and clear obstacles in the yard. The span (the width between the crane’s legs) should be able to cover multiple railcars or truck lanes in one pass.
- Reach: A crane with a longer reach can access more areas within the yard, making it more versatile. This is especially important in larger rail yards or when containers need to be moved over long distances.
Choosing a crane that fits these requirements ensures operational flexibility and enables the crane to serve all parts of the rail yard efficiently.
Rail Yard Layout and Space
The physical layout and space of the rail yard are crucial factors in selecting an RMG crane. The crane should fit comfortably within the yard’s design while maximizing available space for container movement and storage.
- Space Constraints: Rail yards often have limited space, so the crane must be able to operate within those confines. A crane with a narrow track width or a design that allows it to handle multiple tasks in a smaller area will help optimize yard space.
- Operational Footprint: The crane’s design must fit into the yard without obstructing other critical areas like truck lanes, storage zones, or other cranes. Proper planning ensures smooth operations and minimizes the need for expensive modifications to the yard layout.
- Stacking and Storage Areas: Depending on the layout, the crane might need to work in tight spots or need additional height to stack containers efficiently. This is another reason why crane span, lifting height, and reach are so important.
A crane that is well-matched to the rail yard's layout can improve operational efficiency and prevent bottlenecks.
Speed and Efficiency
In high-traffic intermodal yards, speed is essential. The crane must move quickly without sacrificing precision to ensure fast turnaround times.
- Traveling Speed: The crane’s speed when moving along the tracks is crucial for efficiency. Faster speeds mean less time spent moving from one area to another, helping to prevent delays.
- Lifting Speed: The rate at which the crane can lift and lower containers also matters. The faster this happens, the quicker containers can be transferred from railcars to trucks or storage.
- Turnaround Times: High-speed operation helps reduce the waiting time for both railcars and trucks. Faster container transfers can lead to more trucks being serviced per day, which is critical in busy rail yards.
For rail yards with heavy traffic, speed and efficiency are critical to maintaining smooth operations and meeting tight schedules.
Environmental Conditions
Finally, the crane must be designed to perform in the specific environmental conditions of the rail yard. Weather and climate can significantly impact crane performance, so it's essential to consider these factors when choosing the right model.
- Weather Resistance: Wind, rain, snow, and extreme temperatures can all affect crane movement. For example, high winds can make cranes unstable when lifting containers, so certain cranes are designed with stabilizing features for windy conditions.
- Temperature: In areas with extreme temperatures, cranes might need to be equipped with special components (e.g., anti-freeze systems or weatherproofing) to keep them functioning smoothly.
- Other Site-Specific Conditions: Some sites might face challenges like dusty environments, saltwater exposure, or other harsh conditions that could impact crane longevity. Selecting a crane with the right weatherproofing and resistance features ensures long-term durability.
Adapting to environmental conditions ensures the crane can operate efficiently and safely, no matter the weather.
When choosing an RMG crane for intermodal operations, key considerations like operational requirements, rail yard layout, speed, and environmental factors play a critical role. A well-suited crane will meet the load capacity, reach, and speed needed for your operations while also fitting into the yard’s design and handling the local climate.
Factors Affecting RMG Crane Performance in Rail Yards
Selecting the right RMG crane for intermodal rail yards is just the beginning. To ensure the crane performs optimally, there are several factors that can directly impact its efficiency and reliability in real-world operations. Below are the key factors that affect RMG crane performance in rail yards.
Crane Load Capacity and Weight Distribution
The crane’s load capacity is a critical factor in its ability to handle containers efficiently and safely. Rail yards deal with a wide range of container sizes and weights, so it is important that the crane is equipped to handle the heaviest loads expected.
- Maximal Load Handling: The crane must have the capacity to lift the heaviest containers in the yard, whether they are stacked high or spread across the yard.
- Weight Distribution: Proper weight distribution is key to maintaining crane stability, especially when lifting heavy containers at great heights or extending the crane’s reach. Imbalanced loads can cause safety issues and decrease the efficiency of operations.
Crane Stability and Balance
Stability is crucial for safe and effective crane operations, especially when lifting containers at height or moving them across long distances. The design of the crane's undercarriage and legs plays a vital role in preventing tipping or instability.
- Wide Base and Understructure: A crane with a stable base and strong undercarriage ensures that the crane remains grounded, even during high lifts or when handling containers near the edge of the yard.
- Structural Reinforcement: Cranes may need extra reinforcement to handle larger containers or adverse weather conditions like high winds. Ensuring the crane has appropriate structural support helps maintain its balance during operations.
Rail Yard Traffic and Workflow Complexity
The traffic in a rail yard directly impacts crane performance. Busy rail yards often deal with multiple railcars, trucks, and container transfer points, which can create congestion and delays if not managed properly.
- Container Transfer Points: The crane needs to operate smoothly between railcars, trucks, and storage areas without obstruction. Optimizing its travel path and reach helps avoid bottlenecks and maintain a steady flow of containers.
- Queueing and Scheduling: In high-traffic yards, a crane may have to wait for other containers to be moved before it can operate. Efficient scheduling and minimizing waiting times are important for optimizing crane performance and maximizing throughput.
Environmental Impact on Performance
As mentioned earlier, weather and site-specific conditions can have a significant effect on crane performance. Extreme environmental conditions can cause delays, decrease lifting precision, or even damage equipment over time.
- Wind Conditions: Wind speeds can affect crane stability, particularly when lifting containers at high extension. Cranes designed with stabilizers or anti-sway systems can handle windy conditions more effectively.
- Temperature Extremes: Cranes operating in cold or hot climates must be able to function in a range of temperatures without freezing up or overheating. Cold-resistant materials and cooling systems help ensure smooth operation in extreme weather.
- Rain and Snow: Moisture can affect the crane’s electrical systems and moving parts. Weather-resistant designs, like sealed electrical components, can help prevent malfunctions due to rain or snow.
Track Condition and Maintenance Needs
The condition of the rail tracks where the RMG crane operates can impact its performance. Well-maintained tracks ensure smoother, faster travel and reduce wear on the crane’s wheels and undercarriage.
- Track Alignment and Smoothness: Any misalignment in the tracks can cause jerky crane movements, slowing down operations and increasing wear and tear on the equipment. Regular track maintenance and inspections are essential.
- Routine Maintenance: Like any heavy-duty machinery, RMG cranes require ongoing maintenance to stay in peak condition. This includes checking for wear on lifting components, electrical systems, and travel mechanisms.
Operational Safety Features
Safety is always a priority in rail yard operations. Incorporating safety features into crane design can help reduce the likelihood of accidents or operational downtime due to human error or unforeseen circumstances.
- Anti-Collision Systems: With so many moving parts in a busy rail yard, an anti-collision system ensures the crane avoids other equipment and containers, preventing costly accidents.
- Load Monitoring Systems: These systems help operators monitor the weight of the container being lifted, ensuring the crane is not overloaded.
- Emergency Stops and Safety Cut-offs: These systems help prevent further movement if an issue arises, giving operators time to resolve any problems without risk of damage or injury.
7. Operational Training and Operator Experience
Even the best-designed RMG crane requires trained operators who understand the specific demands of the yard and how to maximize the crane’s capabilities.
- Operator Training: A well-trained crane operator can adapt to the yard’s layout, handle container transfers with precision, and minimize errors that could affect efficiency.
- Ongoing Education: As technologies evolve, operators should stay informed about upgrades or improvements to crane systems. Continuous training ensures that the crane’s potential is maximized, and it operates safely within the limits of its design.
Technological Integration
Modern RMG cranes are equipped with advanced automation and control systems that improve performance and efficiency.
- Automated Control Systems: These systems allow for more precise movements, reducing human error and speeding up container handling. Automation also allows for more consistent operations, reducing downtime.
- Integration with Yard Management Systems: Cranes that are integrated with the rail yard’s overall management system can optimize workflow, helping operators make more informed decisions and improve container movement efficiency.
The performance of an RMG crane in a rail yard is influenced by several factors, including crane load capacity, stability, rail yard traffic, environmental conditions, and more. By addressing these factors with appropriate crane selection, regular maintenance, and operator training, rail yard operators can maximize efficiency, safety, and productivity in their intermodal operations.
Customization Options for RMG Cranes
When it comes to rail yards, there’s no one-size-fits-all crane. Every yard has its own layout, container types, and operational needs. That’s where customization comes in. Rail-Mounted Gantry (RMG) cranes are highly adaptable, and tailoring them to fit the specific requirements of your rail yard can make all the difference in improving efficiency, reducing costs, and boosting overall performance.
Let’s break down the key customization options available for RMG cranes:
Adapting to Your Rail Yard's Needs
Every rail yard has its own unique setup. Customizing your crane to fit the layout and container types in your yard helps it work at its best.
- Track Width & Yard Layout: Rail yards can vary in how the tracks are laid out. Some yards have wide tracks, while others are more compact. By customizing the span of the crane, you can ensure it covers the right amount of space and moves smoothly across all tracks.
- Handling Different Containers: Different containers have different sizes and weights. Whether it’s a standard container, refrigerated one, or a larger high-cube container, your crane needs to be able to handle them all. That’s why customizing the lifting system—whether it’s a stronger hoist or a twin-lift system—is important to efficiently manage the variety of containers.
- Reach and Lifting Height: Some rail yards stack containers high, while others deal with long railcars. Customizing the reach and lifting height lets the crane handle all these different scenarios. For example, taller containers or longer railcars may require a crane with more reach and a higher lifting height.
Changing the Crane's Features
Your rail yard may have specific operational demands, and customizing the crane's features can help meet them.
- Crane Dimensions: Depending on the space available, you may need to adjust the crane’s height, width, and ground clearance. These changes help the crane fit into the yard and ensure it can operate without running into space issues.
- Lifting Systems: In some yards, cranes need to handle more than one container at a time. This is where twin-lift systems come in handy. By lifting two containers simultaneously, these systems speed up operations. For yards with heavier containers, stronger lifting systems ensure the crane can handle the load safely.
- Automation: More rail yards are opting for automated cranes to improve efficiency and reduce human error. With automation features like remote control, automated stacking, and smart sensors, the crane can move containers quickly and precisely, all while reducing operational costs.
Power Supply and Efficiency
Another key decision in customizing your crane is choosing the right power source. This decision impacts not just the crane's performance but also its cost and environmental footprint.
- Electric-Powered Cranes: If you want lower operating costs and a cleaner energy source, electric-powered cranes are a great choice. These cranes are efficient and reliable and perform well in long-term operations. The electric system can be customized to meet the specific power needs of your yard.
- Diesel-Powered Cranes: Some rail yards, especially those in remote areas, may not have easy access to an electric grid. For these yards, diesel-powered cranes are the go-to option. Although diesel engines can be more fuel-intensive, they’re flexible and can be customized for better fuel efficiency and longer operating hours.
- Hybrid Systems: If you need a mix of both, hybrid power systems are an option. These systems let you switch between electric power when the crane is stationary and diesel power when it’s moving. This combination offers great flexibility and helps lower fuel consumption.
Sustainability and Energy Efficiency
Today’s rail yards are increasingly focusing on reducing their environmental impact, and customizing cranes for energy efficiency is a big part of that.
- Energy Recovery: Some RMG cranes come with energy recovery systems, which capture and store energy during braking or lowering containers. This helps the crane use less energy, especially in high-traffic areas where cranes stop and start frequently.
- Low-Emission Engines: For diesel-powered cranes, opting for low-emission engines helps reduce air pollution and makes the crane more environmentally friendly. These engines meet emission standards and contribute to cleaner operations.
- LED Lighting: LED lighting is another simple yet effective customization. It uses less energy and lasts longer, providing better visibility in the yard with minimal power usage.
- Solar Power: In sunny areas, some rail yards are installing solar panels on cranes to help power auxiliary systems (like lights and sensors). This cuts down on energy use and makes operations even more sustainable.
Customizing your RMG crane ensures that it performs exactly how you need it to. By adapting the crane’s dimensions, lifting systems, and power sources to fit the unique needs of your rail yard, you’ll improve operational flexibility and efficiency. Plus, with energy-efficient features like solar panels and energy recovery systems, you can reduce costs and support sustainability goals. Whether you’re dealing with a complex layout, high container volumes, or diverse weather conditions, a customized RMG crane helps keep things running smoothly and efficiently.
Maintenance and Longevity of RMG Cranes
When it comes to Rail-Mounted Gantry (RMG) cranes, keeping them in top shape is key to ensuring smooth operations and maximizing their lifespan. Proper maintenance doesn’t just save money in the long run, it also boosts efficiency and safety. Let's break down what you need to know about maintaining RMG cranes for the best performance over time.
Routine Maintenance Needs
Just like any other piece of heavy machinery, RMG cranes need regular check-ups to keep everything running smoothly. Regular maintenance not only prevents breakdowns but also helps to avoid unexpected repair costs.
- Inspections: Regular inspections are essential. Cranes should be checked at specified intervals for signs of wear and tear, such as cracks in the structure or signs of corrosion. These inspections catch small problems before they turn into expensive issues.
- Lubrication: A lot of moving parts in the crane, like the hoists and traveling mechanisms, need proper lubrication to reduce friction and wear. Regular lubrication ensures that the crane moves smoothly and lasts longer.
- Parts Replacement: Over time, certain components like wheels, cables, and brakes wear out. Replacing these parts on schedule ensures that the crane operates efficiently and safely, reducing the risk of downtime.
- Structural Checks: Cranes work hard, and their structural integrity needs to be checked regularly. Routine checks on the frame, gantry legs, and other critical components help to avoid more serious damage, ensuring the crane stays safe to use.
By staying on top of these areas, you can significantly extend the life of your crane and prevent costly repairs down the line.
Cost-Effectiveness of Long-Term Operations
Although investing in the right crane upfront can seem like a big cost, proper maintenance helps offset those costs in the long run by reducing downtime and improving operational efficiency. Here's how:
- Minimizing Downtime: Routine maintenance is the best way to keep your crane up and running. A crane that’s well-maintained doesn’t break down as often, which means fewer interruptions to your operations. This translates into increased productivity and fewer costly delays.
- Lower Repair Costs: Cranes that get regular attention tend to have fewer unexpected repairs. By catching small issues early, you avoid large, expensive repairs that could happen if a problem goes unchecked.
- Long-Term Savings: While maintenance might feel like an added expense, it actually saves money over time. Proper upkeep ensures that the crane performs at its best, and by preventing major issues, it reduces the need for costly emergency repairs.
- Efficiency Improvements: Well-maintained cranes operate more smoothly, use energy more efficiently, and help reduce operational costs. With everything running at peak efficiency, your crane’s performance improves, and you get more value for your investment.
Balancing Upfront Costs with Long-Term Savings
When selecting and maintaining an RMG crane, it’s important to consider both the initial investment and the long-term operational costs. Here’s the deal:
- Upfront Costs: While a high-quality RMG crane might be more expensive at first, it’s an investment that will pay off. A reliable crane that’s built to last can handle heavy workloads over many years, which means you get more for your money.
- Longevity and Efficiency: A well-maintained crane, chosen for the right application, pays for itself by working more efficiently and lasting longer. Opting for a crane that suits your yard’s layout, container types, and workload can reduce wear and tear, saving on parts and repairs.
- Smart Crane Selection: Choosing the right crane from the start can reduce maintenance costs. A crane that’s too big or too small for the job will wear out faster and incur more repair costs. Pick a crane that’s designed for your specific needs to make sure it’s cost-effective in the long run.
Proper maintenance is crucial for maximizing the longevity and performance of your RMG crane. Regular inspections, lubrication, and part replacements are necessary to keep things running smoothly and avoid expensive repairs. Though cranes come with significant upfront costs, proper care and maintenance help reduce downtime, repair costs, and improve efficiency, ultimately leading to long-term savings. In the end, balancing those initial costs with ongoing maintenance will ensure that your crane continues to perform well and save money over time.
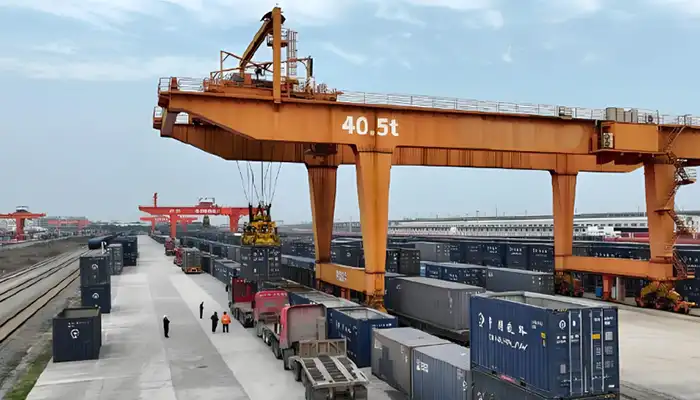
40.5 ton container handling rail mounted gantry crane
Conclusion
When selecting the ideal Rail-Mounted Gantry (RMG) crane for intermodal yard operations, it’s crucial to consider several key factors:
- Crane Features: The crane's capacity, lifting height, span, and reach must be tailored to the specific needs of the rail yard, such as container sizes and handling volumes.
- Operational Considerations: Factors like speed, efficiency, and adaptability to different weather conditions play a major role in ensuring smooth operations.
- Customization Options: Customizing the crane’s dimensions, automation features, and power supply ensures it fits the specific layout and operational requirements of the rail yard, helping maximize space and efficiency.
By choosing the right crane with these elements in mind, rail yard operations can run smoothly and efficiently.
The Role of RMG Cranes in Streamlining Intermodal Logistics
Rail-Mounted Gantry cranes are central to efficient intermodal logistics, providing the perfect solution for transferring containers between railcars, trucks, and storage areas in rail yards.
- Efficiency: The right RMG crane boosts turnaround time by speeding up container handling, improving the flow of operations.
- Cost Reduction: Choosing the right crane can lower both operational and maintenance costs, optimizing the long-term investment.
- Improved Safety: A well-selected crane ensures safer operations by meeting all the environmental and load requirements, minimizing the risks of accidents caused by overloading or poor crane performance.
When you get the crane right, you significantly improve the efficiency, safety, and overall effectiveness of your intermodal logistics.
Selecting the right Rail-Mounted Gantry crane is a decision that impacts the success of rail yard operations for years to come. It’s not just about picking the crane with the best features—it’s about choosing the one that best suits your yard’s unique needs. Whether it's the crane’s lifting capacity, speed, or ability to handle various types of containers, each factor plays a role in optimizing rail yard logistics.
The importance of careful crane selection cannot be overstated. With the right crane, you can ensure smoother operations, enhanced safety, and reduced costs—essential elements for meeting the growing demands of the intermodal transport industry.
Contact to Get Your Customized Railyard Container Gantry Cranes
If you’re looking to improve the efficiency of your intermodal rail yard, the first step is assessing your specific operational needs. Every rail yard is unique—whether it’s the layout, volume of containers, or the types of cargo handled. To ensure you’re making the right investment, consider consulting with crane manufacturers or industry experts who can guide you toward the perfect Rail-Mounted Gantry crane tailored to your yard’s requirements.
- Take the time to review your yard’s container handling needs and space limitations.
- Engage with professionals who understand the intricacies of rail yard logistics.
- Explore customization options that can enhance performance and future-proof your operations.
By consulting with experts, you’ll make a well-informed decision that aligns with both your short-term and long-term goals.Looking ahead, the right crane won’t just be an operational tool; it’ll be a key factor in maintaining competitiveness and meeting the evolving demands of the logistics industry. Stay ahead of the curve by choosing a railway gantry crane solution that’s built to evolve with your needs.
Article by Bella ,who has been in the hoist and crane field since 2016. Bella provides overhead crane & gantry crane consultation services for clients who need a customized overhead travelling crane solution.Contact her to get free consultation.