Selecting Right Control System for Your Crane: A Comprehensive Guide
This guide helps you choose the optimal control system for your crane system for efficient and safe crane operations.
Importance of Control Systems in Crane Operations
Control systems are vital to the safe and efficient operation of cranes. They manage how the crane moves, lifts, and lowers loads, ensuring precision in handling heavy materials. A well-designed control system enhances safety by minimizing the risk of accidents and enabling operators to respond quickly to unexpected situations. Furthermore, these systems contribute to productivity; they allow for smoother operations, reducing downtime and improving overall workflow. Selecting the right control system can lead to enhanced efficiency, lower operational costs, and a safer work environment.
This comprehensive guide aims to assist you in selecting the ideal control system for your crane. It will cover the various types of control systems available, key considerations when making your choice, and the essential features to look for. Additionally, the guide will provide insights into evaluating different control system providers, installation best practices, and ongoing maintenance tips. By following this guide, you will be better equipped to make informed decisions that enhance the performance and safety of your crane operations. Click to check types of crane systems for sale.
Crane Control Systems
Definition of Crane Control Systems
Crane control systems are vital to the operation and safety of cranes, enabling operators to manage the lifting, lowering, and horizontal movement of loads with precision. These systems play a crucial role in ensuring that operations are conducted smoothly and safely, directly influencing productivity and efficiency on the job site. The selection of an appropriate control system can significantly affect load handling capabilities, operator comfort, and adherence to safety protocols.
- Safety Assurance: Modern control systems incorporate advanced safety features such as overload protection and emergency stop buttons, which are essential for preventing accidents and ensuring the safety of both operators and personnel nearby.
- Operational Efficiency: A well-designed control system streamlines workflow by minimizing downtime, enabling faster and more accurate load movements. This efficiency can lead to increased throughput and better use of resources.
- User-Friendly Interface: Many contemporary control systems feature intuitive designs that simplify operations, making it easier for operators to adapt quickly and maintain high productivity levels throughout their shifts.
Types of Control Systems
Manual Control
Manual control systems involve direct manipulation by the operator, using physical controls such as levers, buttons, or joysticks. This traditional method provides a tactile and immediate connection to the crane’s movements, allowing for precise load handling in various scenarios. However, there are several advantages and challenges associated with this approach.
Advantages
- Immediate Response: Operators can respond instantly to changes in load position and environment. This is particularly beneficial for tasks that require fine motor skills and quick adjustments, such as maneuvering loads in tight spaces or during delicate operations.
- Tactile Feedback: The tactile feedback provided by manual controls allows operators to gauge load behavior more accurately. This hands-on approach can enhance the operator's situational awareness and improve decision-making during complex lifts.
- Simplicity and Familiarity: Manual controls are straightforward and often require less technological complexity. Many operators find traditional systems easier to learn and use, especially those with prior experience in similar environments.
Disadvantages
- Operator Fatigue: Prolonged use of manual controls can lead to operator fatigue, which may increase the risk of errors. Physical strain can diminish focus and precision, particularly during long shifts or when handling heavy loads.
- Training Requirements: Extensive training is necessary to ensure operators understand safe practices and can navigate the complexities of different crane models effectively. New operators may require significant time to become proficient, which can impact overall productivity.
- Limited Automation: Manual control systems do not leverage automation features, which can limit efficiency in high-volume operations. As workloads increase, the potential for human error may rise, necessitating the implementation of more advanced control systems.
Typical Applications of Manual Control
Manual control systems are commonly used in various applications, particularly where precision and operator oversight are crucial:
- Construction Sites: In dynamic environments where loads must be maneuvered around obstacles or adjusted frequently, manual control allows operators to respond to real-time conditions.
- Warehouse Operations: For tasks that involve moving goods in tight aisles or adjusting loads on shelves, manual control provides the flexibility needed for careful positioning.
- Maintenance and Repair: Manual control is often employed in maintenance operations where operators need to handle components delicately or navigate complex machinery.
- Specialized Lifts: In applications requiring precise load placement, such as assembling large structures or performing intricate lifts, manual control systems allow for meticulous adjustments.
By understanding the benefits and challenges of manual control systems, operators can better assess their suitability for specific applications, ensuring safety and efficiency in crane operations.
Remote Control
Remote control systems enable operators to manage crane functions from a safe distance, significantly enhancing operational flexibility and safety, particularly in challenging or hazardous environments. These systems typically utilize wireless technology to transmit commands, providing a modern approach to crane operation.
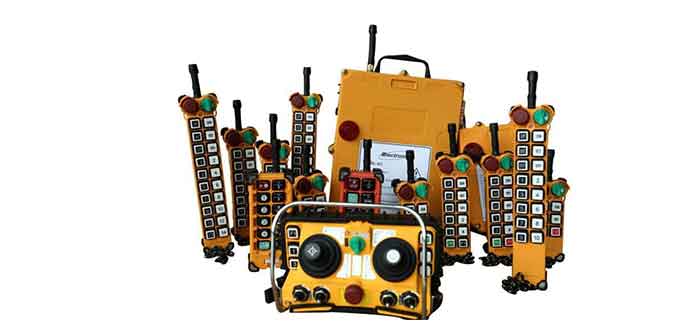
remote control and wireless remote control system
Advantages
- Enhanced Safety: By operating from a distance, workers can maintain a safe perimeter around potentially dangerous loads. This added safety measure is especially important in environments where load shifts or accidents could pose risks to personnel.
- Improved Visibility: Remote operation allows operators to position themselves where visibility is optimal, enabling them to see the load and surrounding area more clearly. This is crucial in tight spaces or complex environments, where line-of-sight issues can complicate maneuvering.
- Operational Flexibility: Remote control systems offer greater flexibility in crane operation. Operators can easily reposition themselves as needed, adapting to changes in the work environment without being physically tethered to the crane.
Considerations
- Reliability of Wireless Connection: The reliability of the wireless connection is essential to prevent accidental loss of control. It’s vital to choose systems with robust connectivity features, such as dual-band frequency options or fail-safe mechanisms, to maintain stable communication between the operator and the crane.
- Training Requirements: Operators should undergo thorough training to become proficient with the specific features and functions of the remote control system. Understanding how to handle the technology effectively is crucial for ensuring safe and efficient operations.
- Potential for Signal Interference: Operators must also consider the potential for signal interference in certain environments, such as industrial sites with heavy machinery or areas with physical obstructions. Selecting systems designed to minimize these risks can enhance reliability.
Typical Applications of Remote Control
Remote control systems are well-suited for various applications, particularly in situations that demand increased safety and flexibility:
- Construction Sites: In construction, where cranes often lift heavy materials over active work areas, remote control allows operators to manage lifts while staying clear of hazards.
- Hazardous Environments: In settings such as chemical plants or waste disposal facilities, remote control systems enable operators to manipulate loads without being exposed to potential dangers, like toxic substances or falling debris.
- Heavy Equipment Operation: Remote controls are ideal for operating heavy machinery in rugged terrain, allowing operators to maintain a safe distance while managing operations effectively.
- Specialized Lifting Operations: For tasks requiring precise placement of loads, such as in assembly lines or manufacturing settings, remote control systems enhance the operator's ability to maneuver loads accurately without compromising safety.
By leveraging remote control systems, operators can enhance safety, improve visibility, and adapt to changing conditions in various crane operations, ultimately leading to more efficient and effective outcomes.
Cabin Control
Cabin control systems involve operating the crane from a dedicated cab located on the crane itself. This setup provides operators with a centralized location for controls and enhances their ability to monitor the load and surrounding area closely, making it a popular choice for various lifting operations.
Advantages
- Enhanced Visibility: The cabin design typically includes large windows and strategic positioning, allowing operators to maintain a clear view of the load and the operational environment. This visibility is critical when navigating complex spaces or coordinating with ground crews.
- Centralized Control: The control panel within the cabin integrates multiple functions, such as load monitoring, movement controls, and safety features. This centralized control setup enables operators to manage crane operations more effectively, especially when handling large or heavy loads that require precise maneuvering.
- Comfort and Safety: Cabin control systems often prioritize operator comfort, featuring ergonomic seating and controls that minimize strain during operation. This focus on comfort helps reduce fatigue, allowing operators to maintain concentration over extended periods.
Considerations
- Ergonomic Design: It is essential that the cabin is ergonomically designed to reduce operator fatigue. This includes comfortable seating, appropriate control placement, and sufficient space for movement within the ca An ergonomically sound cabin can significantly enhance operator performance and safety.
- Regular Maintenance: Regular maintenance of both the control systems and visibility aids, such as cameras or sensors, is crucial for optimal performance and safety. Scheduled inspections ensure that all systems function correctly and that the operator has the necessary visibility to perform their duties safely.
- Environmental Controls: Consideration should be given to environmental controls within the cabin, such as climate control and ventilation systems. Maintaining a comfortable temperature and air quality can enhance operator focus and reduce fatigue.
Typical Applications of Cabin Control
Cabin control systems are ideal for various applications, particularly in environments that demand high levels of visibility and control:
- Heavy Construction: In construction projects involving large structures or heavy materials, cabin control allows operators to efficiently manage lifts while maintaining oversight of surrounding activities.
- Industrial Facilities: In manufacturing or processing plants, cabin-controlled cranes can facilitate the handling of heavy machinery parts, ensuring precision in assembly or maintenance tasks.
- Shipping and Ports: In shipping yards, cabin control systems enable operators to efficiently load and unload containers, providing them with the necessary visibility to navigate complex port operations.
- Mining Operations: In mining, where cranes are often used to lift heavy equipment or materials, cabin control systems enhance safety and operational efficiency by allowing operators to maintain a close watch on their surroundings.
By utilizing cabin control systems, operators can enjoy enhanced visibility, centralized control, and increased comfort, leading to more efficient and safer crane operations in a variety of settings.
Key Considerations for Selecting a Control System
Load Capacity and Type of Crane
When selecting a control system for a crane, understanding the load capacity and the specific type of crane is paramount. Each crane type, whether it be an overhead crane, gantry crane, or mobile crane, has distinct operational requirements that significantly influence the choice of control system.
Load Capacity
The control system must be fully compatible with the crane’s maximum load capacity to ensure safe and efficient operation.
- Compatibility Issues: Using a control system designed for lighter cranes with a heavier model can lead to serious operational failures. This mismatch could result in equipment malfunction, compromised safety, and potentially dangerous situations for personnel nearby.
- Operational Safety: A control system must be able to handle not just the maximum load but also dynamic loads that can occur during lifting operations. Factors such as load sway, wind resistance, and sudden stops should be taken into account when assessing load capacity.
- Manufacturer Specifications: Always refer to the manufacturer’s specifications for both the crane and the control system. This will help ensure that all components work together seamlessly and meet safety standards.
Type of Crane
Each crane type has unique characteristics that influence its control needs based on design and intended application.
- Mobile Cranes: These cranes often operate in dynamic environments where the ability to move freely is crucial. A remote control system can enhance maneuverability by allowing operators to adjust the crane’s position from a safe distance. This setup is particularly beneficial in construction sites where visibility may be obstructe
- Overhead Cranes: For overhead cranes, a cabin control system may be more effective. This type of control provides operators with a centralized location to manage various functions while maintaining direct visibility of the load and surrounding are It is particularly advantageous in industrial settings where precision is critical.
- Gantry Cranes: Gantry cranes may require a hybrid approach, utilizing both manual and remote control systems, depending on the application. For example, when moving large components in a manufacturing facility, operators may need the precision of cabin controls combined with the flexibility of remote operation for repositioning.
By thoroughly evaluating both the load capacity and the type of crane, operators can select a control system tailored to their specific operational needs. This careful consideration will lead to enhanced safety, improved efficiency, and better overall performance in crane operations.
Application Environment
The environment in which a crane operates plays a crucial role in determining the most suitable control system. Understanding whether the crane will be used indoors or outdoors, as well as identifying potential hazards, is essential for making an informed decision.
Indoor vs. Outdoor Use
Cranes used indoors typically face fewer environmental challenges compared to those operating outdoors.
- Indoor Cranes: These cranes can generally accommodate a wider range of control systems due to controlled conditions. Factors such as temperature, humidity, and exposure to elements are less variable, allowing for the use of standard control systems without specialized protection.
- Outdoor Cranes: Outdoor cranes are exposed to varying weather conditions, which necessitates the selection of more robust control systems. These systems should be designed to operate reliably in different temperatures, high humidity, and exposure to rain, snow, or extreme sunlight.
- Weather-Resistant Features: When selecting a control system for outdoor use, look for features such as sealed enclosures, weatherproof components, and UV-resistant materials to ensure longevity and reliable performance under harsh conditions.
Hazardous Environments
For cranes operating in hazardous areas, such as chemical plants, oil refineries, or construction sites, special considerations are paramount.
- Explosion-Proof Features: It is crucial to choose a control system that includes explosion-proof features. These systems are designed to prevent ignition of flammable materials in the surrounding environment, ensuring the safety of operators and personnel.
- Compliance with Safety Standards: The selected control system must comply with industry-specific safety standards and regulations. This may include certifications such as ATEX (for explosive atmospheres) or IECEx (for electrical equipment in hazardous areas), ensuring that the system meets stringent safety requirements.
- Risk Assessment: Conducting a thorough risk assessment of the operational environment can help identify specific hazards that the control system must address. This assessment will guide the selection of necessary safety features and compliance requirements.
By carefully considering the application environment, operators can select a control system that not only meets the operational demands of the crane but also enhances safety and reliability in various conditions. This thoughtful approach will contribute to more effective crane operations and reduce the risk of accidents.
User Experience and Training Needs
Operator experience is a critical factor in determining the most suitable control system for a crane. Evaluating user familiarity with various control methods can help in selecting a system that enhances both efficiency and safety.
Operator Familiarity
Understanding the level of operator familiarity with different control systems is essential for effective crane operations.
- Leverage Existing Skills: If operators are already trained on specific control systems, opting for a similar system can be advantageous. This minimizes the need for extensive retraining and allows operators to apply their existing skills, leading to quicker adaptations and smoother operations.
- Reduced Error Rates: Familiarity with controls can significantly decrease the likelihood of mistakes during operations. Operators who are comfortable with the system are more likely to make quick, accurate decisions, thereby improving overall productivity and safety.
- Feedback from Operators: Engaging with operators during the selection process can provide valuable insights. Their input can highlight preferences and concerns, helping to choose a system that aligns with their comfort levels and enhances their performance.
Training Requirements
It is essential to consider the training needs associated with different control systems, as these can vary significantly.
- Complexity of Systems: More complex systems, such as automated controls or advanced remote controls, may require extensive training programs. These systems often come with multiple features and functions that operators must understand to use them effectively and safely.
- Comprehensive Training Programs: Investing in thorough training can lead to better operator performance and reduced risks of accidents. A structured training program should cover not only the technical aspects of operating the control system but also safety protocols, emergency procedures, and troubleshooting techniques.
- Ongoing Training and Support: Continuous education is important, especially as technology evolves. Providing ongoing training sessions and refreshers can help operators stay up-to-date with new features or upgrades in the control system, ensuring that they remain proficient and confident in their skills.
By carefully assessing user experience and training needs, organizations can select a control system that not only meets operational demands but also supports operator proficiency and safety. This thoughtful approach ultimately contributes to enhanced crane operations and a safer work environment.
Key Considerations for Selecting a Control System
Regulatory Compliance and Safety Standards
Adhering to local and international regulations is a vital consideration when selecting a crane control system. Compliance with established safety standards not only protects operators but also mitigates liability risks for employers.
Safety Standards
Different industries are governed by specific safety regulations that must be strictly followe
- Industry-Specific Regulations: For instance, cranes used in construction must comply with Occupational Safety and Health Administration (OSHA) regulations, while those in manufacturing may need to meet International Organization for Standardization (ISO) standards. Understanding these requirements is crucial to ensure that the selected control system aligns with legal obligations.
- Certification Requirements: It is essential to verify that the control system comes with necessary certifications. These may include CE marking for compliance with European safety standards or ANSI standards for equipment in North Americ Choosing certified products enhances credibility and ensures adherence to safety protocols.
- Documentation and Record-Keeping: Maintaining thorough documentation of compliance is important for audits and inspections. Keep records of all certifications, training programs, and safety inspections related to the control system.
Regular Inspections and Maintenance
Establishing a comprehensive maintenance schedule for the control system is critical for ongoing compliance and safety.
- Scheduled Inspections: Regular inspections should be conducted to ensure that all safety features of the control system are functioning correctly. This includes checking emergency stop functions, overload protection systems, and any integrated safety devices.
- Preventive Maintenance: Implementing a preventive maintenance program can help identify and address potential issues before they lead to failures or accidents. This proactive approach contributes to the longevity of the control system and enhances overall operational safety.
- Compliance Audits: Periodic audits of compliance with safety standards should be performed to ensure that all regulations are being met consistently. Engaging third-party auditors can provide an objective assessment and identify areas for improvement.
By prioritizing regulatory compliance and safety standards, organizations can select a crane control system that not only enhances operational efficiency but also safeguards the well-being of operators and minimizes legal risks. This commitment to safety and compliance fosters a culture of responsibility and excellence in crane operations.
Features of Modern Control Systems
Ergonomics and User Interface
The design of modern crane control systems emphasizes ergonomics to enhance operator comfort and efficiency. A well-designed user interface can significantly reduce fatigue and improve accuracy during operations.
- Ergonomic Design: Controls should be positioned to minimize strain on the operator’s body. Features such as adjustable seating, intuitive control placement, and easy-to-reach buttons are essential for long-term comfort.
- User Interface: A clear and straightforward user interface, often with touchscreen displays, allows operators to quickly access essential functions. Visual indicators for load weight, movement speed, and operational status help operators make informed decisions rapidly, enhancing overall performance.
Advanced Safety Features
Safety is a paramount concern in crane operations, and modern control systems incorporate several advanced safety features to mitigate risks.
- Emergency Stop Functions: These critical features enable operators to immediately halt crane operations in case of an emergency. Emergency stop buttons should be easily accessible from all operating positions, allowing for quick intervention during potentially dangerous situations.
- Overload Protection: This feature prevents the crane from lifting loads beyond its rated capacity, significantly reducing the risk of accidents. Overload protection systems typically include alarms and visual alerts to notify operators when they are approaching or exceeding weight limits, ensuring safe handling of materials.
Connectivity and Integration with Other Systems
Modern control systems often include connectivity features that facilitate integration with other equipment and systems, enhancing overall operational efficiency.
- Wireless Connectivity: Many systems support wireless communication, allowing for real-time data exchange between the crane and other machinery. This capability is particularly useful in automated environments where multiple machines operate in sync.
- Integration with Monitoring Systems: Control systems can be integrated with monitoring solutions that track performance metrics, load conditions, and maintenance needs. This data helps operators optimize operations and schedule preventive maintenance, ensuring the crane remains in peak condition.
- Compatibility with Fleet Management Systems: For companies operating multiple cranes, integrating control systems with fleet management software can streamline operations. This integration provides insights into usage patterns, maintenance schedules, and overall performance, leading to more effective resource management.
Evaluating Control System Providers
Researching and Comparing Manufacturers
When selecting a control system provider, thorough research is essential to ensure you choose a reputable manufacturer that meets your operational needs.
- Manufacturer Reputation: Investigate the track record of different manufacturers in the crane control system market. Look for companies with a long history of reliability and innovation, as well as those known for producing high-quality products.
- Product Range: Consider the variety of control systems offered by each manufacturer. A provider with a diverse product lineup can better accommodate specific requirements, whether you're looking for manual, remote, or cabin control systems.
- Certifications and Standards: Check if the manufacturer’s products comply with relevant safety and industry standards. Certifications from recognized organizations can indicate a commitment to quality and safety in their designs.
Understanding Warranty and Support Services
A solid warranty and reliable support services are crucial factors when evaluating control system providers, as they can significantly impact the long-term performance of your crane.
- Warranty Coverage: Review the terms of the warranty provided by the manufacturer. A comprehensive warranty should cover parts and labor for a reasonable duration, protecting your investment against defects and ensuring peace of min
- Technical Support: Investigate the availability and responsiveness of the manufacturer’s technical support team. Efficient customer service can provide assistance during installation, troubleshooting, and maintenance, helping to minimize downtime.
- Training Programs: Some manufacturers offer training programs for operators and maintenance personnel. These programs can enhance safety and efficiency by ensuring that users are fully acquainted with the system’s features and operational procedures.
Customer Reviews and Case Studies
Examining customer feedback and case studies can provide valuable insights into the performance and reliability of control systems from different providers.
- Customer Reviews: Look for reviews and testimonials from other companies that have used the control systems. Pay attention to feedback regarding performance, ease of use, and any challenges encountere Reliable feedback can help you gauge the real-world effectiveness of the systems.
- Case Studies: Review case studies that highlight specific applications of the control systems in various industries. These examples can illustrate how different solutions have addressed particular challenges and achieved successful outcomes, helping you determine if a provider's systems are well-suited to your needs.
- Industry Recommendations: Seek recommendations from industry peers or professional networks. Insights from experienced users can guide you toward reputable manufacturers and inform your decision-making process regarding the best control system for your crane operations.
Implementation and Installation
Installation Best Practices
Proper installation of the crane control system is critical for ensuring optimal performance and safety. Following best practices can help prevent issues down the line.
- Site Assessment: Conduct a thorough assessment of the installation site before beginning. This includes evaluating space, power supply, and environmental conditions to ensure compatibility with the control system.
- Professional Installation: Engage qualified technicians for the installation process. Skilled professionals can ensure that all components are correctly set up and configured, minimizing the risk of malfunctions.
- Documentation: Keep detailed documentation of the installation process, including wiring diagrams and system configurations. This information will be invaluable for future maintenance and troubleshooting.
- Safety Checks: After installation, perform comprehensive safety checks to ensure that all components are functioning correctly and that safety features, such as emergency stops and overload protection, are operational.
Training and Familiarization for Operators
Training is essential for maximizing the effectiveness of the control system and ensuring safe operation. A well-structured training program can enhance operator competence and confidence.
- Comprehensive Training Programs: Develop a training program that covers all aspects of the control system, including operation, safety features, and troubleshooting. This program should be tailored to the specific needs of your operators.
- Hands-On Experience: Incorporate practical, hands-on training sessions where operators can practice using the control system in a controlled environment. This experience helps reinforce learning and build familiarity with the equipment.
- Refresher Courses: Schedule regular refresher courses to keep operators updated on any system changes or new features. Continuous education ensures that all personnel remain proficient in operating the control system safely and efficiently.
Maintenance and Troubleshooting Tips
Regular maintenance and proactive troubleshooting are key to prolonging the life of the control system and ensuring smooth operations.
- Maintenance Schedule: Establish a routine maintenance schedule that includes regular inspections, cleaning, and servicing of all components. This schedule should follow the manufacturer’s recommendations for maintenance intervals and procedures.
- Troubleshooting Protocols: Develop clear troubleshooting protocols that operators can follow in the event of a malfunction. This should include common issues, diagnostic steps, and contact information for technical support if neede
- Documentation of Issues: Maintain a log of any issues encountered, along with the steps taken to resolve them. This documentation can help identify recurring problems and inform future maintenance efforts, improving overall system reliability.
- Parts Replacement: Keep a supply of critical replacement parts on hand to reduce downtime in the event of a failure. Knowing which components are most likely to require replacement can help streamline the maintenance process.
In selecting the right control system for your crane, several key considerations come into play. First, understanding the various types of control systems—manual, remote, and cabin control—allows for an informed choice based on specific operational needs. Evaluating factors such as load capacity, application environment, user experience, and regulatory compliance is essential for ensuring safety and efficiency. Additionally, modern control systems offer features like ergonomic designs, advanced safety mechanisms, and connectivity options that enhance overall functionality. Finally, researching manufacturers, understanding warranty and support services, and considering customer feedback are crucial steps in finding a reliable provider.
Choosing the right control system for your crane is a critical decision that impacts safety, efficiency, and overall operational success. Investing time in research, training, and proper implementation can lead to significant long-term benefits, including enhanced productivity and reduced risks. By prioritizing ergonomics, safety features, and ongoing support, you can ensure that your crane operations run smoothly and effectively. Ultimately, the right control system not only optimizes performance but also contributes to a safer work environment for all personnel involve
Article by Bella ,who has been in the hoist and crane field since 2016. Bella provides overhead crane & gantry crane consultation services for clients who need a customized overhead travelling crane solution.Contact her to get free consultation.