Reliable, High Quality Hoist and Cranes for Hazardous Environment
Custom crane, Processed Crane & Automatic Crane for
Explosive, Corrosion , Space Constraint & Harsh Applications
Custom cranes and processed cranes for hazardous, explosive, corrosion, space constraint, harsh environment & heavy duty applications,etc. Working in explosive environments demands a wide range of lifting equipment, from standard hoisting equipment to cutting-edge solutions. As a result, we've tailored our overhead material handling solutions to meet your individual, and frequently unique, lifting requirements. All crane components are chosen to meet the high standards of safety necessary in hazardous environments such as chemical and petrochemical industries, oil refineries, gas power plants, wastewater treatment plants, paint shops, and other industrial locations.
In harsh and hazardous environments, safety comes first.
Material handling products that are reliable and high-quality, and can withstand even the hardest conditions.
Keeping people and hoist and crane equipment safe in tough and hazardous conditions is not only necessary, but crucial to many companies' and industries' operations. Hazardous conditions can be found within a chemical plant, a petrochemical operation, or a steel mill. To get the tasks completed safely and in conformity with hazardous environment rules, regulations, and standards, you'll need specially designed hoisting equipment. We can offer what you need to help you solve the material handling equipment.
Hazardous Environment Expertise You Can Trust
Customers all over the world prefer our Overhead Crane Systems because of their comprehensive portfolio of explosion-proof lifting, drive, and control technologies. For explosion-proof and hazardous environment applications, we also offer a wide variety of services, from consulting and engineering through country-specific administration of licensing and certification procedures.
Reliable, High Quality Hoist and Cranes for Hazardous Environment
Explosion Proof , Spark Proof & Flame Proof Overhead Crane for
Explosive Hazardous Environment
Explosion Proof Environment Need for Spark Resistance Lifting Equipment
Potentially flammable atmospheres can create a unique set of issues for material handling equipment in a variety of industries, ranging from upstream oil and gas and refining to agricultural and woodworking. Material equipment and most employees can all be endangered in these conditions.
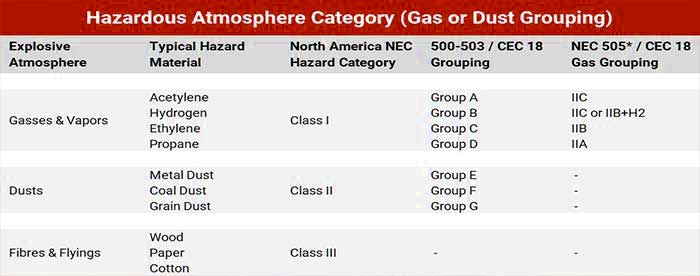
Spark Resistance's Importance
The hazardous areas are mainly divided into two types of explosive atmospheres: those involving flammable gases and those involving explosive dusts. These hazard Classes are further subdivided into Group and Division.
It is common knowledge that friction between some materials can produce enough sparks to ignite combustible gas or particles. An old flintlock musket or a cigarette lighter are both examples of this. Obviously, the kind and concentration/dilution of gases in a given location influence the likelihood of a mechanically generated source igniting, but other important considerations could include:
- The types of materials that come into contact with one other
- The speed/pressure with which the materials come into contact
- Corrosion on one or more of the touching surfaces
- Lubrication
Sparks can also be created when steel surfaces come into contact. Most hoists and cranes employ steel for load-bearing components such hooks, lower blocks, load chain, and trolley wheels. As a result, most lifting equipment is ineffective in dangerous conditions.
Explosion Proof Hoist, Winch, Crane System
To reduce the risk of sparking, consider non-sparking materials such as copper, bronze, and austenitic stainless steel for coatings or as material substitutes for material handling overhead and crane equipment. These materials are not only spark resistant, but also corrosion resistant. Surface corrosion can increase friction between mating components, hence corrosion prevention is crucial when lifting in hazardous settings.
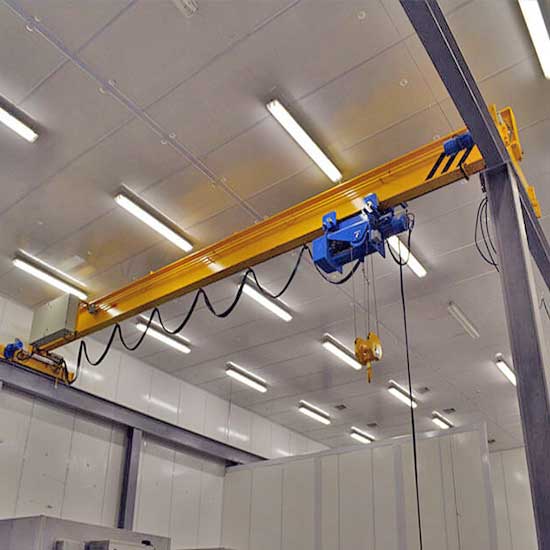
1 Ton, 5 Ton,10 Ton Explosion Proof Single Girder Overhead Cranes
Explosion proof single girder overhead crane is for mining, oil, gas, dusty applications, featured as spark proof, flame proof & explosion proof.
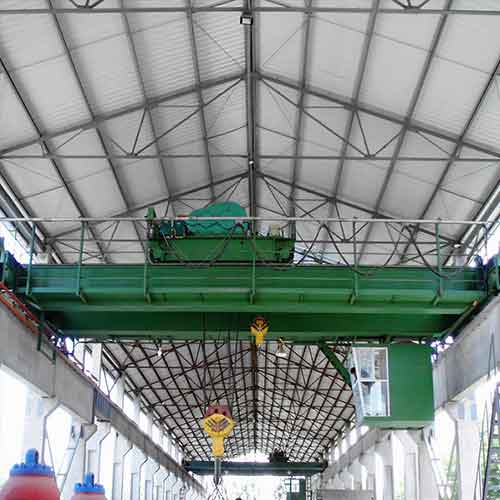
5 Ton - 75 Ton Explosion Proof Double Girder Overhead Crane
5 ton -75 ton explosion proof double girder overhead cranes for workshops with flammable or explosive gases. Explosion-proof grade: EXdIIBT4 and EXdIICT4.
Reliable, High Quality Hoist and Cranes for Hazardous Environment
Custom Overhead Travelling Cranes & Hoists for
Corrosion, Salty & Moist, Acid & Other Chemical Applications
Environment Needed for Corrosion Resistance Hoist & Cranes
Lifting equipment used in classified hazardous locations must comply with the national and or other related appropriate standards. Mechanical spark resistance for key components such as load blocks, hooks, trolley wheels, load brake, and lifting mediums such as chain and wire rope should also be ensured in these places. In these environments, corrosion resistance for lifting equipment is just as vital as spark resistance to maintain the safety of employees, equipment, and the facility itself.
Corrosion resistance hoist and crane for outdoor harsh weather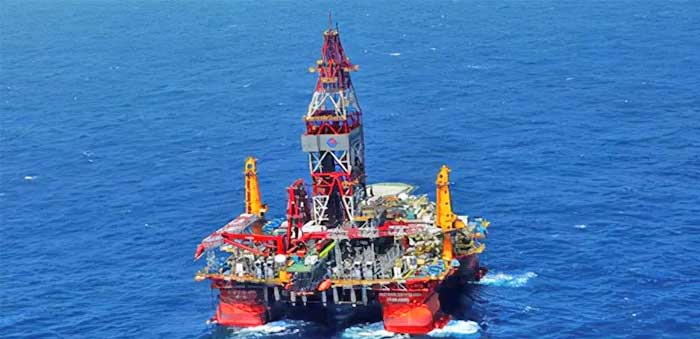
There are many classified hazardous areas outside that expose lifting equipment to direct and often harsh weather. This includes, to name a few, offshore oil platforms, natural gas processing plants, and refineries. Equipment in offshore facilities, in particular, may be subjected to splash zones, salt spray, and the condensation of salt-laden air. Sulfur, mineral acids, and other corrosive agents are frequently present in the crude oil and natural gas that is produced, processed, and transported in these facilities, further corroding lifting equipment used in these environments.
Corrosion can be extremely expensive, costing billions of dollars each year in the oil and gas industry alone. The cost of repairing and replacing corroded lifting equipment, combined with unscheduled maintenance, downtime, and lost production, can have a significant impact on these businesses' profitability. Corroded load blocks, hooks, chains, and cables can also lead to catastrophic equipment failure. This can not only cause costly damage to equipment and the facility, but it can also injure or even kill operators and other people in the facility.
So how do you protect lifting equipment from corrosion?
The use of corrosion-resistant materials for load blocks, hooks, chains, cables, and other components is critical. Furthermore, because surface corrosion can increase friction between mating components, corrosion prevention is important in maintaining mechanical spark resistance when using these products in classified hazardous environments.
Always look for lifting solutions made of spark- and corrosion-resistant materials and coatings. Meet with a lifting application engineer to determine which solution is best for your application and whether a custom solution is required.
Corrosion-Resistant Features Include:
- Solid bronze hooks, bottom blocks, and trolley wheels
- Lightweight aluminum housings
- Stainless steel load and hand chain
- Epoxy finishes with multiple coats
- Corrosion-resistant zinc-aluminum finish
In addition to corrosion-resistant materials and finishes, proper hoist lubrication is required to avoid sparking. These measures, combined with a robust inspection and preventative maintenance program that includes pre-lift inspections, play a critical role in ensuring the dependability and safe operation of lifting equipment in these harsh environments.
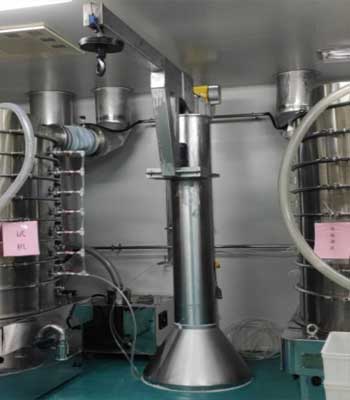
Crome-plated jib crane and stainless jib crane for clean room
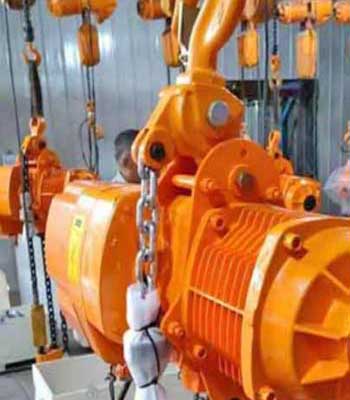
Galvanized chain hoist for underwater use
Reliable, High Quality Hoist and Cranes for Hazardous Environment
Low Headroom Hoists & Cranes & Portable Cranes for
Space Constraint & Limited Applications
Space Constraint Challenges
Hazardous places are usually found in restricted spaces or with limited space, particularly in the mining and oil and gas industries. In regions where there is coal or other combustible particles, mining tunnels frequently have limited overhead clearance. Offshore facility designers in the oil and gas industry usually attempt to keep overall structure sizes as small as possible, which can lead to low headroom between deck levels and tight clearances for monorails and crane runways.
Compact overhead lifting equipment with low headroom and short side clearances, as well as a short "end approach" to maximize the deck covering area served by the monorail hoist or crane, are required in all of these scenarios.
The requirement for small hoists, trolleys, and cranes is frequently challenged by the presence of combustible gases or dust in the places where the equipment is employed. Explosion-proof and spark-resistant characteristics may be required, each providing its own set of issues due to the limited space available.
Electric motors and control enclosures used in hazardous areas are typically larger and heavier than those used in non-hazardous areas. With the same safe working load, spark-resistant bronze load blocks and hooks are typically larger than carbon or alloy steel hooks and blocks. Because stainless steel has a lower tensile strength than alloy steel, the use of spark-resistant stainless steel load chain or wire rope frequently necessitates de-rating the equipment capacity. This downsizing can lead to larger, heavier, and more expensive hoists and cranes. Consult an application specialist whenever possible, and make certain that operators are thoroughly trained in hazardous lifting applications.
Lifting Hoist & Crane Solutions for Hazardous Environments with Space Limitations
When specifying or purchasing lifting equipment for hazardous locations with limited space, there are numerous factors to consider. When environmental dimensions compete with the need to comply with hazardous area requirements, the safety of personnel, equipment, and facilities must always take precedence in your decision making.
Fortunately, there are a variety of equipment options available that can be used in confined spaces, including spark- and corrosion-resistant materials and explosion-proof components. Low-headroom hoists are available in wire rope and chain varieties, as well as manual, electric, and pneumatic models.
Wire rope hoists have higher capacities and faster lifting speeds, whereas chain hoists have smaller overall dimensional envelopes to optimize end approach and clearance. Although solid bronze and stainless steel components can provide long-lasting protection against sparking and corrosion, copper or nickel plating can be used in some applications to provide lower headroom dimensions and reduce the need for de-rating of safe working loads.
We provide a wide range of additional services for explosion-proof and hazardous environment applications, ranging from consulting and engineering to country-specific management of approval and certification procedures.
Whatever your industry or location, we have the hoists, cranes, and application expertise to keep your people, materials, and equipment safe in hazardous and corrosive environments.
Reliable, High Quality Overhead Travelling Cranes for Hazardous Environment
Custom Crane, Processed Crane & Automatic Crane for
Heavy Duty & Harsh Applications
Harsh Environment needs for Processed Crane & Automatic Cranes
For various industrial applications, such as steel mill, wast handling, mining, refinery, and paper pulp and many other industries, where heavy duty material handling required for 24 hours operation, or hazardous loads such as hot ladle or hot steel products are required for safe handling or where hazardous gas or dust may appear, the custom cranes and automatic crane are needed.
Automatic Crane
Automation of overhead cranes. When managing even the most massive loads, your overhead crane system is absolutely important to the daily function of your company. Consider how much more efficient this procedure could be.
Not only may automating your crane system save your overall production costs, but it can also improve your facility's safety and productivity. With 34 years experiences, we will assist you in developing an unique crane system for your company that meets even the most stringent lifting needs.
Custom Crane
we understand that there's no "one size fits all" in lifting. Many industries require individually designed cranes tailored for specific factory processes and business needs. So we offer custom cranes optimized to operators' precise requirements. As needs change, so can the cranes, upgraded and modernized. Custom cranes often use standard products in unique ways, with new design elements for specific purposes.
Reliable, High Quality Hoist and Cranes for Hazardous Environment
Custom Crane, Processed Crane & Automatic Crane for
Various Types of Hazardous Applications
With over 34 years in the business, we've fabricated new cranes of all types and sizes. Our custom fabrications can be found in the factories and warehouses of a wide array of industries such as aerospace, steel manufacturing, automotive, mining facilities, distribution centers and many more.
Your Trusted Overhead Travelling Crane Manufacturer & Supplier